Abstract In CCMT2016, tool manufacturers from abroad, Isca, Mapa, Lanzi, Mitsubishi, Tailuo, No., Hanmo, Kyocera, and Xiongke, from the domestic tool industry, drill, quantity, quantity, Ha Yigong, Dalian Far East, Chengdu Industrial Research Institute, Zhangzhou Aoketai, Su...
At CCMT2016, tool manufacturers from abroad, Isca, Mapa, Lanzi, Mitsubishi, Tailuo, No., Hanmo, Kyocera, and Xiongke, from the domestic tool industry, drill, quantity, quantity, ha Yigong, Dalian Far East, Chengdu Industrial Research Institute, Zhangzhou Aoketai, Suzhou Arnold, Wuxi Fanginch, Suzhou Karma, Beijing Wald, Changshu Wanke, Changzhou R&F, Chengdu Fengyi, Harbin Zhongtian, Mianyang Miangong Dozens of companies including Ningbo Sanhan, Wuxi Tainuo, Zhuzhou Keli, Zhejiang Shangyou, Wuxi Smika, and agents Shangya have formed the main lineup of the exhibition tool exhibition area. This article only briefly describes the key new products and technical levels of this CCMT tool exhibition area as follows. First, the car knife
Many manufacturers exhibited new turning tool materials, blade inserts or turning structures at CCMT2016.
Iska's new products in the car can be said to be the combination of the three. In terms of materials, ISK exhibited the IC6025 (Fig. 1) for machining stainless steel, and the carbide grades IC806 and IC804 for high temperature alloy turning and grooving (Fig. 2).
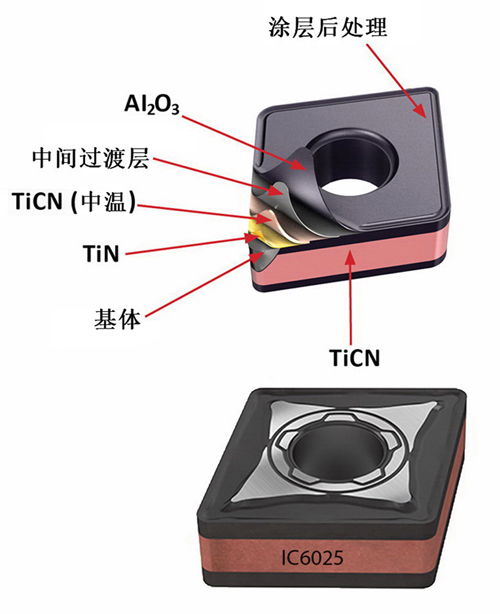
Figure 1 Isca's IC6025
IC806 is coated with a titanium-titanium (TiAlN, PVD) coating on an ultra-fine grain substrate and subjected to a beam-coating treatment. It has better wear resistance and significantly improves tool life and reliability. IC804 is in its The uncoated material IC4 was coated with an aluminum titanium aluminum (AlTiN) coating and subjected to a special post-coating treatment to significantly improve tool life and reliability. Compared with the two, the wear resistance of IC804 is higher and the toughness of IC806 is slightly better. 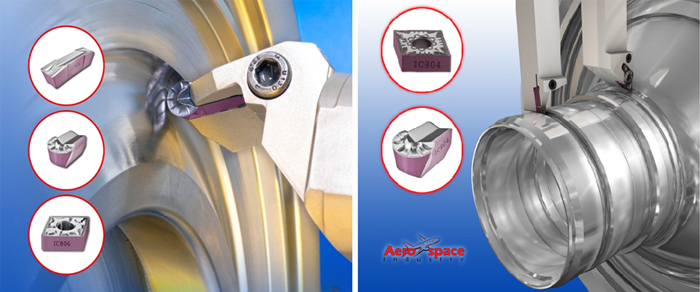
Figure 2 Isca's IC806 (left) and IC804 (right)
Mitsubishi Materials also exhibited two materials for turning, the UE6120 (Fig. 3) known as the "opening coating" and the MP735 known as the "Grounding Coating". 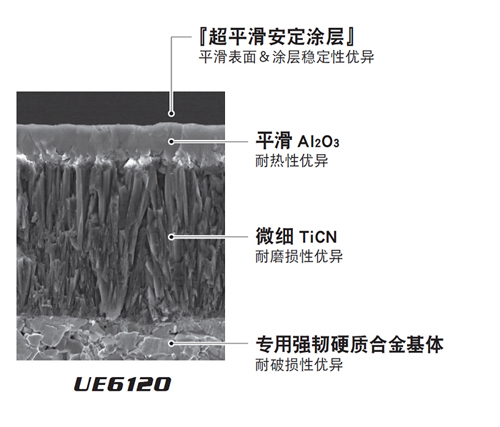
Figure 3 Mitsubishi Materials UE6120
Zhuzhou Diamond, the leading manufacturer of domestic carbide cutting tools, exhibited a new structure of its CNC blade grade system at CCMT. The cutting materials include YB7315 (Fig. 4), diamond YB9320 and silver diamond YB6315. 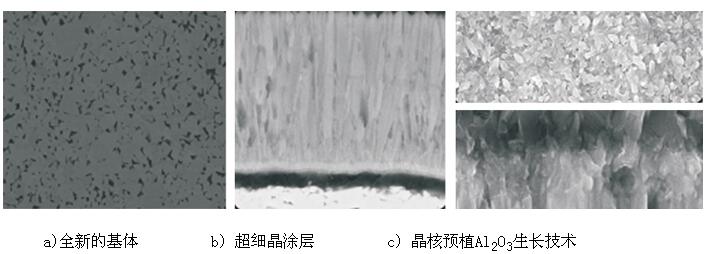
Figure 4 Zhuzhou Diamond YB7315
Zhangzhou Aoketai exhibited its AC150P material at this exhibition. AC150P base material adopts special modification technology, which has uniform structure, stable performance and excellent softening resistance under high temperature conditions. It adopts special coating post-treatment process to extend the service life of the blade and improve the smoothness of the workpiece. 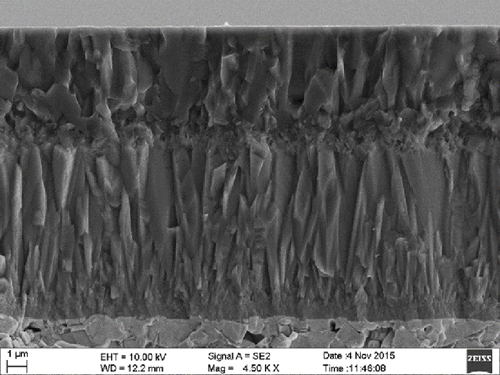
Figure 5 Electron microscopy of Zhangzhou Aoketai AC150P
In terms of the chipbreaker shape of the turning tool, it is always possible to see some new trough shapes that are difficult to find without careful inspection. The shape of the turned steel parts exhibited by Iskar is divided into R3P, M3P and F3P (Figure 6). 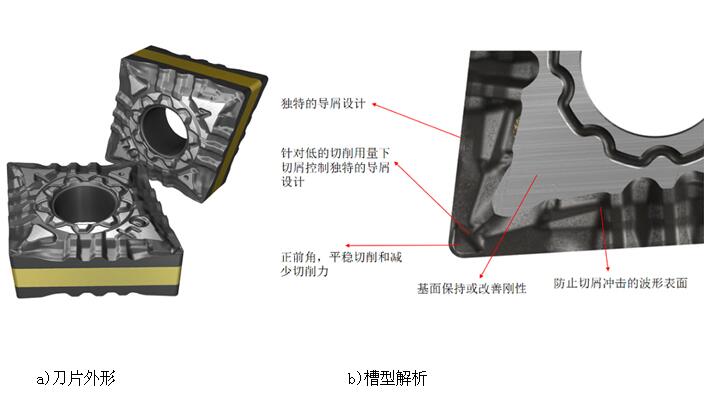
Figure 6 Isca F3P steel parts finishing groove
On the grooving turning tools for small parts, Iskar has introduced a number of innovative products. Due to its small size and compact structure, there are not many optional tools in this area, and there are few new technologies. Iskar's new products provide more choices for small parts turning. Figure 7 shows Iskar's Swiss automatic lathe high pressure cooling series with coolant directly to the cutting edge of the insert. 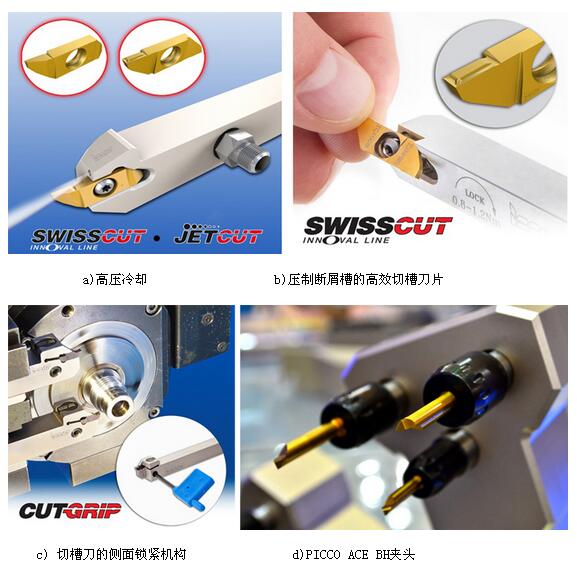
Figure 7 Iskar's Swiss automatic lathe tool series
Iskar also exhibited new products in heavy-duty cutting tools. Considering heavy-duty grooving, ie heavy-duty turning - the most vulnerable part of the cutting area in the grooving process, Iskar designed a unique tool holder (see the large circle below Figure 8), this heavy-duty grooving tool change Simply replace the tool holder instead of replacing the tool body or blade.
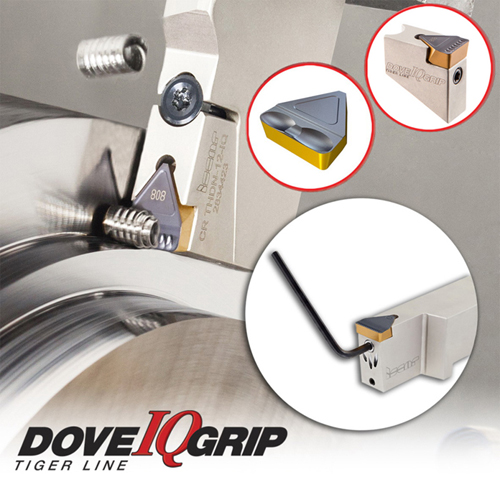
Figure 8 Isca's DOVEIQ GRIP
Second, milling cutter In terms of milling cutters, we first introduce Mitsubishi materials' indexable milling cutter WSX445 (Fig. 9). This type of milling cutter features a double-sided insert that can have a large rake angle and multiple effective cutting edges. This design has a positive effect on the guide vanes, the curling of the chips is more reasonable, and it is not easy to damage other cutting edges that are not used.
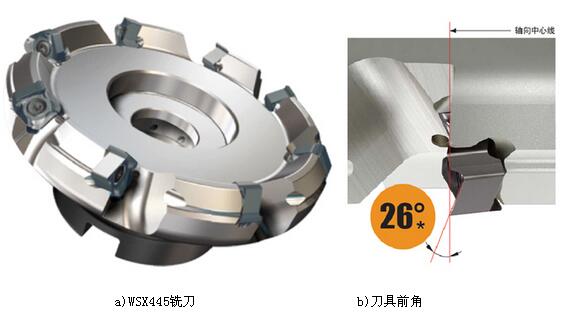
Figure 9 Mitsubishi Milling Cutter WSX445
The second type of milling cutter to be introduced is the face milling cutter FMAX (Fig. 10) for efficient finishing of Mitsubishi materials. This type of milling cutter has three technical features: the first is the locking mechanism, the second is the adjustment mechanism, and the third is the cooling structure. The coolant body is arranged close to the nozzle hole along the rake face, which can effectively prevent the front. Mullage is generated on the blade surface. 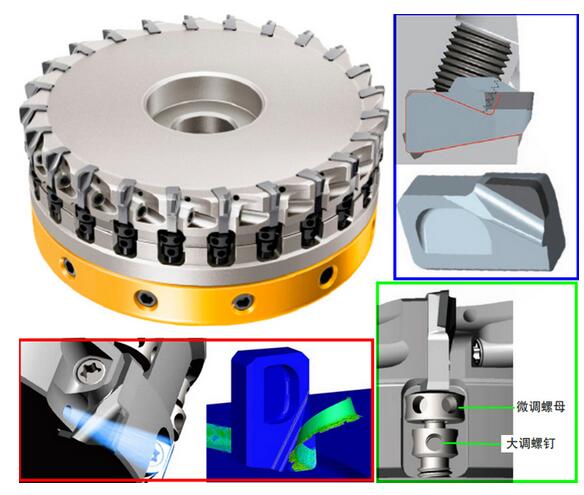
Figure 10 Mitsubishi FMAX milling cutter (the basket is the locking mechanism, the green frame is the adjustment mechanism, and the red frame is the cooling structure)
Marpa also exhibited the new face milling cutters FlyCutter and EcoMill-Blue with diamond inserts (Fig. 11). The FlyCutter cutter head, which is mainly used for small spindles (such as BT30), uses an aluminum cutter body to reduce the moment of inertia when the cutter head rotates at high speed, and removes a considerable part of the cutter body in front of the cutter teeth, which is beneficial to further reduce the tool weight and moment of inertia. It also facilitates the chipping during cutting, ensuring that the chip space is not blocked before the cutter teeth are separated from the cutting section, ensuring the safety of the machining. EcoMill-Blue sets a small temporary chip space on the tool holder, and there is no chip residue on the surface of the workpiece, making the subsequent cleaning process very simple and easy. 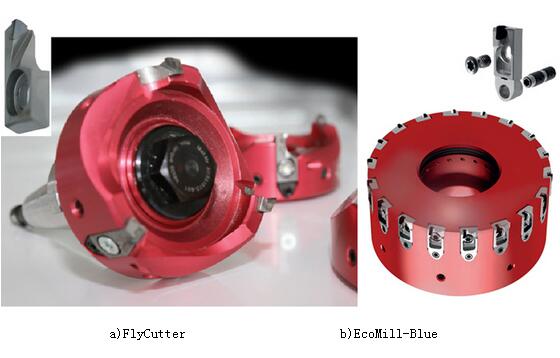
Figure 11 Mpa's two PCD face milling cutters and their tool holders
Iskar introduced the HELIDO 800 milling cutter (Fig. 12), the cyclone milling cutter and the Ingersoll milling cutter. The HELIDO 800 milling cutter can be used to mount a square insert with a deeper depth on the same cutter body, or an octagonal insert with a slightly smaller depth but double the number of edges. 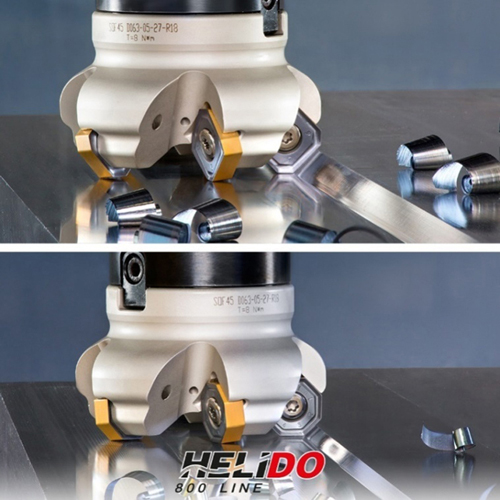
Figure 12 Iskar's HELIDO 800 milling cutter
Germany's Blue Flag exhibited its new copy milling cutter CopyMax2 (Fig. 13). The CopyMax2 features two full-featured cutting edges that can be indexed and reused when the first cutting edge wears and have the same tool life as the first cutting edge. 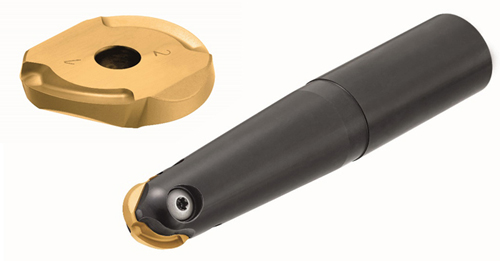
Figure 13 Blue Flag's CopyMax2 milling cutter
The company has exhibited its micro-path end mill system DS (Fig. 14). The new end mill series offers a superior geometry for ultra-fine surface quality. 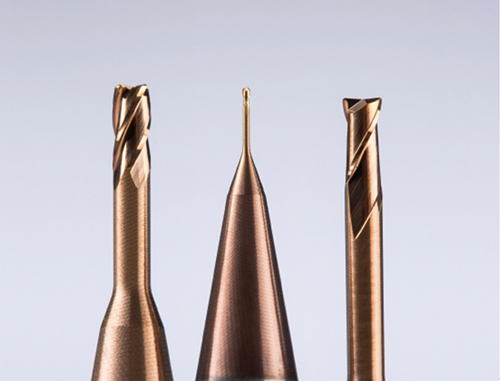
Figure 14: Micro-diameter milling cutter
Third, hole machining tools In terms of hole machining tools, Dalian Far East exhibited a variety of high-speed steel drills with its Cleveland brand.
Iskar's IQ Chameleon 700 series (Figure 15) is also eye-catching. The series is uniquely designed to be self-locking by elastic deformation of the slotted part of the carbide tip without the need for any other locking screws and other accessories.
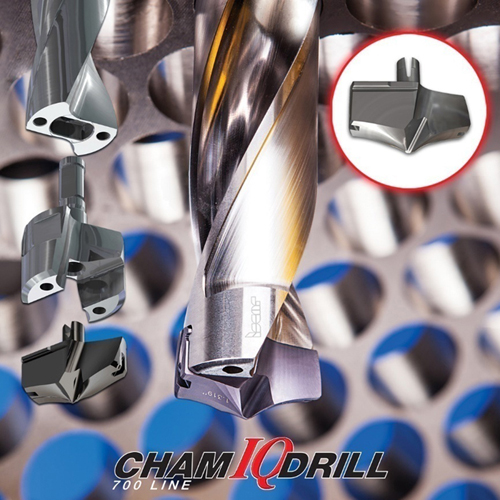
Figure 15 Iskar's IQ Chameleon Drill 700 Series
Shang Ya exhibited the three-blade Tritan-Drill from MILLER (Figure 16). It is said to have high centering and is suitable for the processing of through holes and broken holes; by cutting the chisel edge, reducing the cutting force and processing heat. 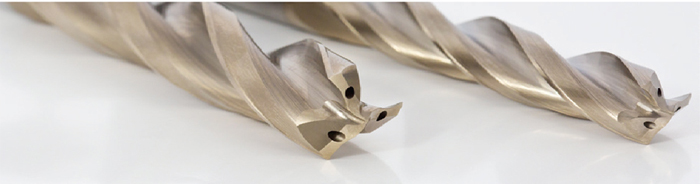
Figure 16 MILLER Tritan-Drill three-edged drill
Recently, 3D printing has become a hot topic in the manufacturing industry. Many people are worried about the impact of additive manufacturing, including 3D printing, on the tool industry for reduced material manufacturing. The two products on the Marpa booth gave us an answer: 3D printing is not a “rice bowl†that grabs the tool, but can be used to make tools that we could hardly manufacture, thus enriching the specifications of the tool. Figure 17 is a Marpa 3D printed interchangeable bit QTD. Using 3D printing technology, the processing problem of the spiral inner cold hole and even the spiral shaped inner cold hole (the left side of the small figure in the upper right corner of Fig. 17 is a triangular inner cold hole) can be solved. 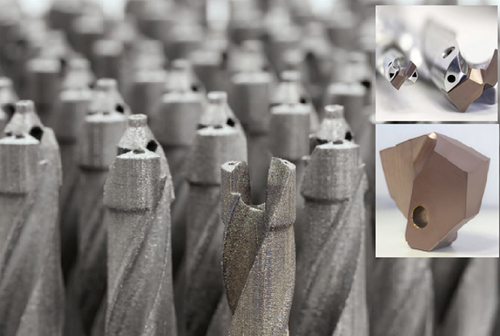
Figure 17 Marpa uses a 3D printed interchangeable bit QTD
Composite processing is one of the fastest growing industries in recent years. Marpa exhibited a lot of composite processing tools at this exhibition. Since the processing of composite materials is a relatively new field, many tool users and service providers are not comprehensive enough to understand the composite materials. Mapa's composite crown drill (ie, head changer) can simplify the use of multi-tools. Generally, no sharpening is required. After the cutting edge of the drill is blunt, the crown (ie the head) can be replaced. Processing process. 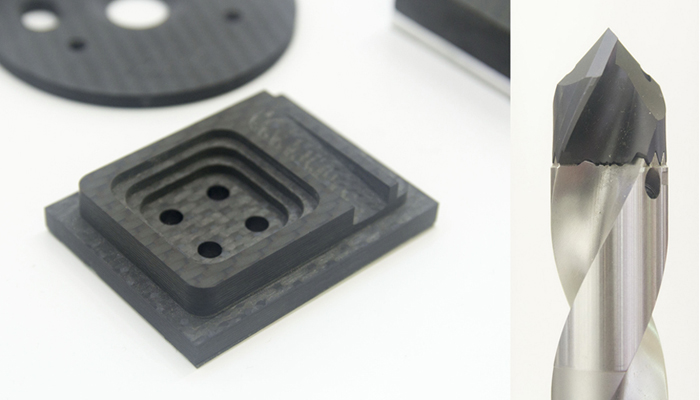
Figure 18: Mako exhibits composite workpieces and interchangeable drill bits for processing composite materials
Marpa also exhibited a nesting drill for composite drilling. For this nesting drill, Marpa explained that this is not because the user needs to save material, reduce cutting power, leave the core for sampling, etc. for the purpose of using conventional nesting drills, but to reduce chips. Wuxi Fanginch exhibited a rough boring tool that is applying for a utility model patent. It uses the action of the tilting tooth to reasonably transfer the cutting resistance to the boring body according to the design direction, which reduces the influence of cutting resistance on the positioning between modules. Thereby improving the stability of the file during the cutting process.
Shanghai Songde also exhibited their micron-sized boring tools and vibration-reducing boring tools (Fig. 19). The adjustment accuracy of the micro-scale boring tool is increased to a radius of 0.5 m per grid and a diameter of 1 m. The product won the "CCMT 2016 Spring Yan Award" from the China Machine Tool Industry Association.
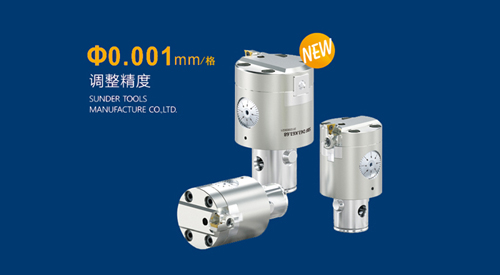
Figure 19 Shanghai Songde's micron grade file
Another eye-catching product on the Shanghai Songde booth is the vibration-damping boring tool, which effectively solves the problem of long-excession tool cutting chattering, especially in deep-hole machining. Shanghai Songde studied the dynamic vibration damping technology and damping damping technology, designed and developed a unique damping damping system and its structural form, which helps to accurately minimize the amplitude of the tool vibration. At the same time, the cutting vibration is studied. The flutter control technology facilitates accurate determination of vibration types in different fields and effectively controls these vibrations. 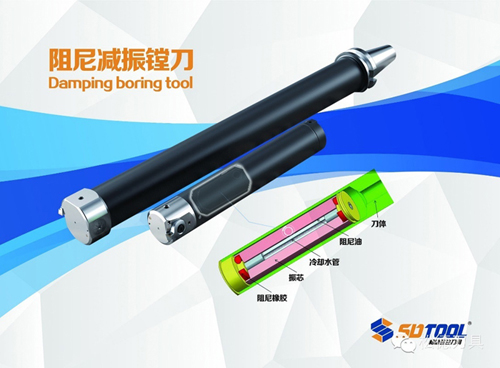
Figure 20 Shanghai Songde Damping Damper
Fourth, thread, gear processing tools In terms of threaded tools, ISK exhibited an IQ five-point double-end threaded cutter with 10 cutting edges (Fig. 21). According to Iskar, the insert uses its universal alloy grade IC908, which has a significantly longer life of threaded inserts. Compared to the common three-blade flat-mounted threaded inserts, the insert increases the number of cutting edges; the cutter body is designed with internal cooling passages. Suitable for conventional cooling processing, also suitable for high-pressure cooling processing; the position of the blade is simple and convenient, the operator can perform the indexing operation on the machine tool without removing the blade locking screw (excluding the face change), so it can be realized. No downtime."
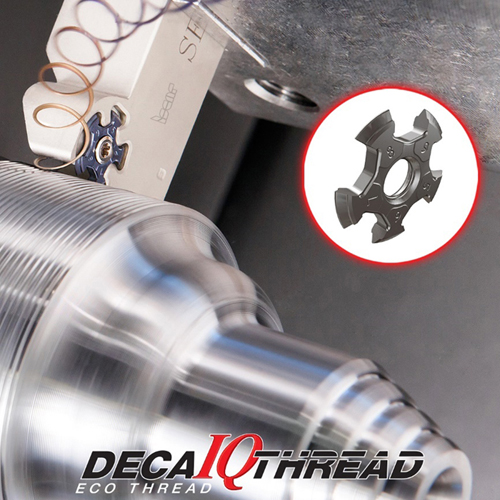
Figure 21 Isca IQ five-point double-head thread turning tool (DECA-IQ-THREAD)
Suzhou Karma exhibited a special thread milling cutter for petroleum valves. According to Karma, the tools used for petroleum valve parts must be able to adapt to harsh working conditions and ensure safety and reliability. Under such conditions, the thread milling cutter must overcome the difficulty of large jump and large vibration to ensure that the milling cutter does not chip and break during the cutting process, and the machined thread does not have a bell mouth phenomenon. 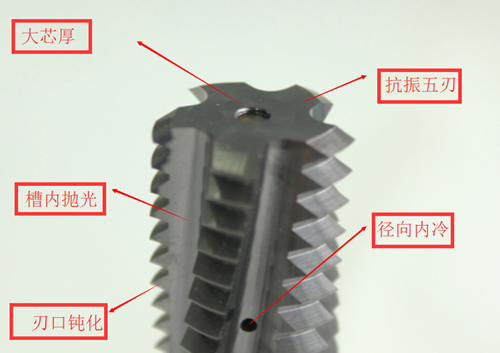
Figure 22 Suzhou 锑玛 oil valve special thread milling cutter structure
Chengdu Chengquan Tools exhibited three special taps developed by it. The first is a special tap for automobile wheels, the second is a special tap designed for processing difficult-to-machine materials such as austenitic stainless steel, and the third is a high-hard steel tap for hardened materials with a hardness of 45~52HRC. 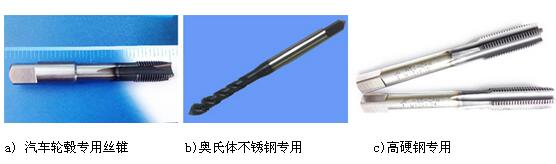
Figure 23 3 special taps for the Chengdu tool
In terms of gear cutters, the German blue flag exhibited a hob-chamfering compound knife. This tool can be designed for rough rolling, chamfering and fine or coarse rolling, chamfering and precision machining according to the requirements of gear machining. Up to IT6-7, it can replace the original shaving process, and the chamfering processing efficiency is 30% higher than the original process, and the investment of the chamfering machine is eliminated, which greatly reduces the production cost and equipment investment. This tool is suitable for processing small modulus gears in the automotive industry, as well as gear processing for large modulus and multi-number of gears in wind power, construction, crane, military and other industries. 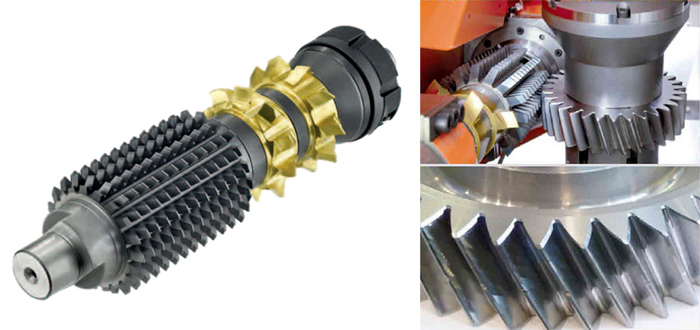
Figure 24 Blue-grid roll-to-cutter system, processing status and results
Ha Yigong also exhibited an indexable gear hob, which was assembled into a hob by a multi-piece tool holder module and two side flanges. Suitable for high speed and efficient machining of large modulus gears before grinding or grinding. In addition to the indexable gear hob, Ha Yigong also exhibited indexable gear milling cutters, including indexable gear roughing cutters, indexable semi-finished gear milling cutters and indexable precision gear milling cutters.
The German horn has also exhibited a gear milling cutter. Similar to its disc-shaped saw blade milling cutter, it is divided into a head-integrated, multi-tooth single-row and multi-tooth double-row.
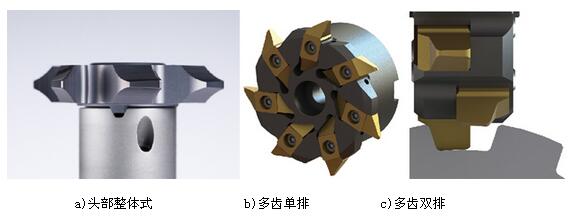
Figure 25 Gear milling cutter from Germany
Five, forming processing tools Forming tools are one of the key features of tooling solutions. At the CCMT2016 exhibition, many manufacturers, especially the domestic tool manufacturers, exhibited quite a lot of forming tools.
Ha Yigong exhibited an indexable rotor slot milling cutter and an indexable grooving broach. The former is a specialized and specialized tool, which is the most ideal tool for machining all kinds of rotor slots of large motors. The latter is highly versatile and has a rectangular broaching groove type, which is suitable for rough broaching of forming grooves such as keyways or gutters, and is especially suitable for grooving broaching in the steam turbine industry.
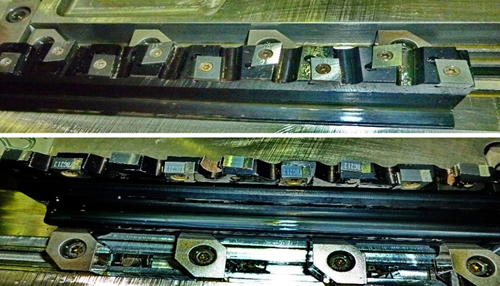
Figure 26 Harbin Yigong's indexable grooving broach
Suzhou Arnold exhibited its overall tooling solution for crankshafts and connecting rods and forming tools for engine cylinder head and hydraulic valve block machining. In Arnold's crankshaft monolithic tooling solution, the 30x aspect ratio ultra-long solid carbide drill bit is particularly eye-catching and has reached a similar high level as foreign countries. Arnold also exhibited several other advantageous products. 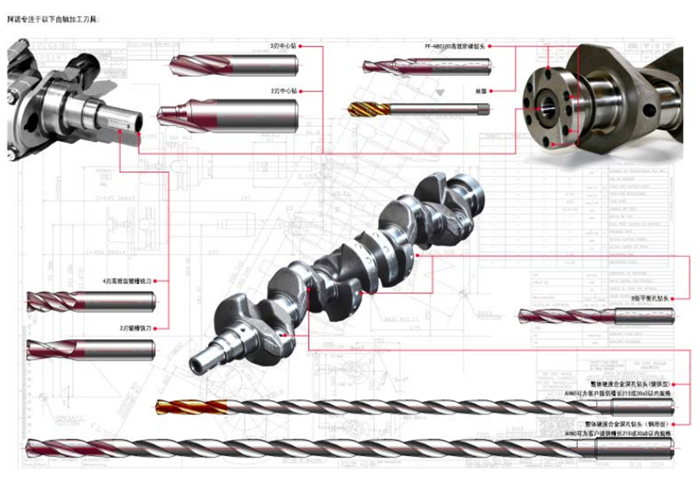
Figure 27 Suzhou Arnold's crankshaft overall tool solution
Wuxi Fanginch also exhibited a variety of forming tools. Figure 28 is a case study of a solution for the "rail" of a high-pressure common rail system part of a diesel engine, including the outer circumference of the vehicle and the return port of the flat, milled external thread and the car parts. Through the forming and compounding, the processing time and the tool change time are reduced, the processing efficiency of the user is greatly improved, and the economic benefit is more remarkable. 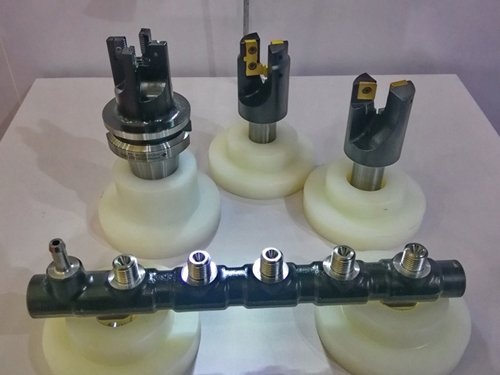
Figure 28 Wuxi square inch solution for diesel engine high pressure common rail system parts "rail"
Sixth, the tool system In terms of tool systems, Hammer, Germany, exhibited a Cool Flash holder with a safety lock (SafeLock). Within a few years, Hammer has introduced a safety lock technology holder that prevents the tool from being pulled out of the chuck and a waterfall cooling handle that features a cutting fluid that is close to the tool. This CCMT exhibits these two items. Technology combined with the shank.
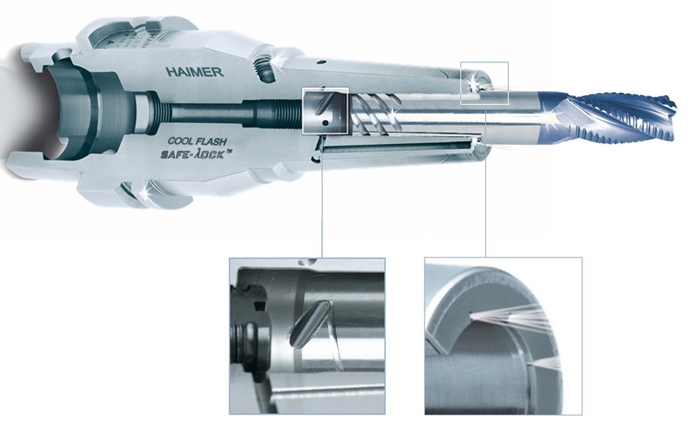
Figure 29 German Hammer's waterfall handle with safety lock
Marpa and Shangya exhibited hydraulic chucks with 3D printing. For the economics of 3D printing hydraulic chucks, Marpa said that because their 3D printing is in the mode of continuous production day and night, the cost is not high, and its price is not much different from the traditional manufacturing hydraulic chuck. 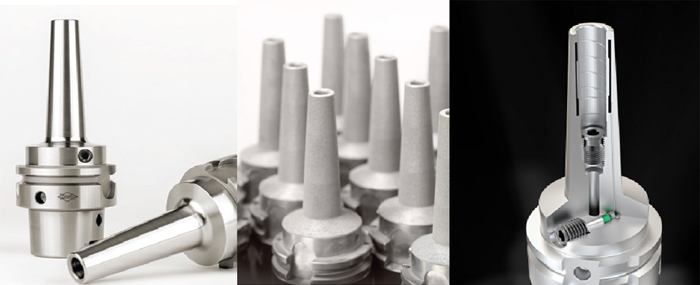
Figure 30 Hydraulic chuck with 3D printing
Luoyang Xincheng is a professional manufacturer of rivets in China. In addition to China's standards, international standards, German standards, American standards, Japanese standards and other relatively large road products, the exhibition also includes Mazak, Mitsui series of nails, South Korea's Samsung horizontal machining center pull nails And special pull nails for German giant wave machine tools. (China Machine Tool Industry Association Tool Branch Yang Xiao wrote) Elevator Cabin Modernization, Elevator Cab Modernization, Elevator Car Modernization
It is common for an elevator's mechanical systems to still be in good shape while the car interior is worn and outdated. Our car modernizations bring the interior up to date with a range of modern and durable design options and accessories.
Elevator Cabin Modernization |Replacement
Replacement of an existing cabin with a new one. Choice can be made from the complete wide range of CEP cabins.
Elevator Cabin Modernization, Elevator Cab Modernization, Elevator Car Modernization
CEP Elevator Products ( China ) Co., Ltd. , https://www.zjfullelevatorreplacement.com