The gear is an important part of the reducer, and its quality and performance have a major impact on the entire reducer. Choosing the right materials and formulating reasonable process measures are important prerequisites for improving the load carrying capacity and service life of the reducer. 17Cr2Ni2MoA is widely used in hardened gear reducers due to its good hardenability and comprehensive mechanical properties.
A certain type of hardened surface reducer produced by our company has a gear material of 17Cr2Ni2MoA. During the user's use, the pinion gear with the modulus of 3mm and the number of teeth of 20 frequently breaks the tooth, which causes the whole reducer to fail, which has a very serious impact on our company and users. In response to this problem, we conducted an in-depth analysis of the 17Cr2Ni2MoA gear teeth.
1. Microstructure observation
The microstructure of the gear was observed using an optical microscope and a scanning electron microscope. Figure 1 shows the low-magnification microstructure of the gear from the surface to the core, and Figure 2 shows the high-magnification of the gear from the surface to the core. The microstructure of the gear surface and the core was observed by SEM, as shown in Fig. 3 and Fig. 4. Considering the microstructure and SEM observation, the outer surface of the gear is martensite, the core is bainite, and the intermediate transition zone is martensite + bainite.
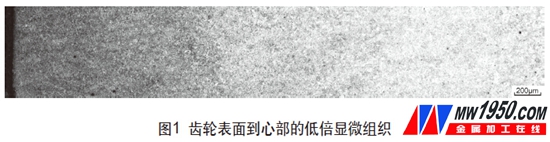
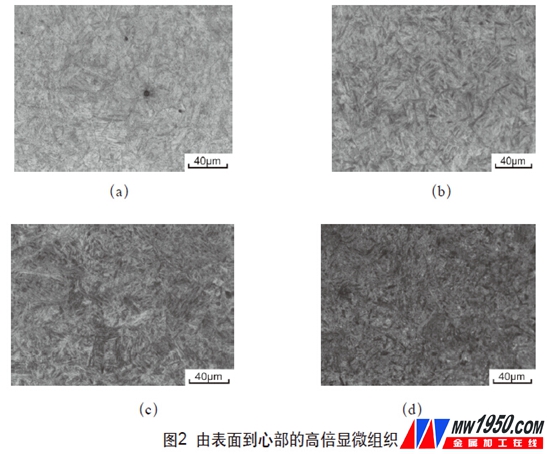

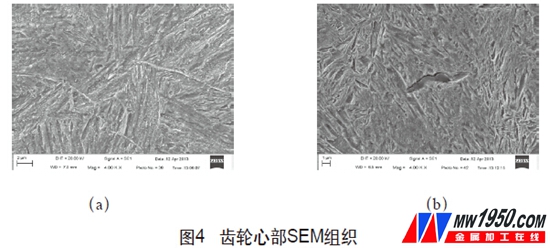
During the observation of the microstructure by SEM, obvious inclusions were observed on the sample, and the number was large, and most of them were less than 10 μm, but more than 10 μm. The inclusions were analyzed by SEM energy spectrum analysis. The results of the energy spectrum are shown in Figure 5, which indicates that the inclusions are dominated by Al2O3 and MgO inclusions.
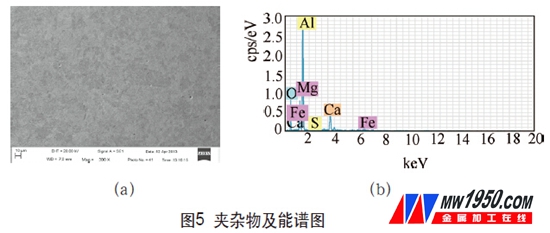
2. Fracture morphology observation
The fracture morphology of the gear was observed by SEM, as shown in Fig. 6. Judging from the fracture condition, it is mainly brittle fracture. There are cracks on the fracture surface, the original metallographic structure of the surface material is not good, the performance is brittle and the toughness is small.
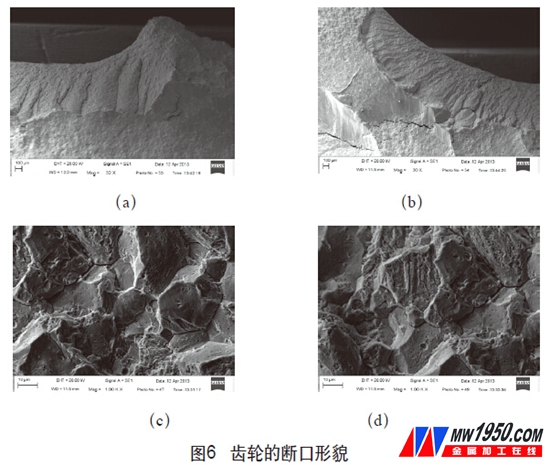
3. Cause analysis and improvement measures
It can be seen from the above analysis that the main cause of the gear tooth breakage phenomenon of this reducer is the excessive inclusion of raw materials and surface cracks. The specific improvement measures are as follows:
(1) When purchasing gear steel, purchase refined steel that meets the metallurgical quality requirements of gear steel.
(2) The forging ratio should be ensured during processing. The forging ratio of rolled steel is greater than 3, and the forging ratio of continuous casting steel is greater than 5.
(3) When the tooth is carburized, in order to prevent the penetration layer from being too deep, the brittleness of the tooth after quenching increases, the toughness is reduced, and the depth of the layer is reduced by about 0.2 mm.
(4) Appropriately reduce the quenching hardness of the gear to prevent excessive brittleness of the tooth. The surface hardness of the tooth was reduced from 58 to 62 HRC to 55 to 58 HRC, and the core hardness was reduced from 30 to 42 HRC to 36 to 40 HRC.
(5) Do not grind the root (ie the bottom of the tooth groove) when grinding the teeth to prevent the root strength from decreasing due to the tooth thickness reduction and the grinding crack.
(6) The profile of the high-speed gear tooth tip is modified to reduce the meshing interference and impact of the gear teeth and improve the lubrication state of the tooth surface. By adopting the above measures, our company has re-produced this type of reducer, and the 17Cr2Ni2MoA small gear broken tooth phenomenon has been improved, which has improved the load-bearing capacity and service life of the reducer, and has been recognized by users.
4. Conclusion
Through the observation and preliminary analysis of the microstructure and fracture morphology of the 17Cr2Ni2MoA reducer gear, the causes of the gear teeth breaking phenomenon of the reducer are found, and the specific improvement measures are proposed. The above analysis provides an important theoretical basis for us to control the quality of gear raw materials and process improvement. By adopting measures such as controlling raw material quality, improving heat treatment and machining process, the load capacity and service life of the reducer are improved.
About the author: Lu Hui, Hebei Tianze Heavy Machinery Co., Ltd., Process Technology Department.
3Pc Ball Valve,3 Pc Ball Valve,3Pc Body Ball Valve,3Pc Flanged Ball Valve
Wenzhou Dico Valve Technology Co.,Ltd. , https://www.dicovalves.com