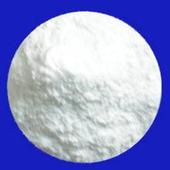
As far as the soda industry is concerned, the focus of emission reduction is ammonia-alkali waste liquor. The reduction of ammonia-alkali waste liquor is a worldwide problem and the industry’s most troublesome disease. According to reports, every cubic metre of soda ash produced will produce 10 cubic meters of waste liquid. If dry ashing technology is used, the discharge of waste liquid will be reduced, but 7.5 to 8 cubic meters of waste liquid will be discharged for each ton of soda ash produced. Although this is currently the best level of emission reduction in the world, emissions are still huge. Due to the large amount of processing and high costs, the common practice in foreign countries is also direct emissions. Although the ammonia-alkali enterprises have adopted many measures such as recovering salt and cobalt chloride from the waste liquid and using the ammonia residue for flue gas removal, the effect is not good due to too large processing volume and high cost. This involves not only the technical and financial problems, but also the issue of the whereabouts of recycled materials.
At present, domestic production of calcium chloride amounts to 1 million tons, and most of it comes from the recovery of soda ash waste liquid. Half of this is for export and half is consumed domestically. The potential for the production of calcium chloride from ammonia-alkali waste liquids is high. If all ammonia liquids are recovered, the annual production of calcium chloride will reach 5 million tons. Although some domestic companies are struggling to produce calcium chloride with ammonia-based waste liquid, they are not able to produce benefits because they are both energy-consuming and costly, and they are very difficult to expand and develop. In response, Wang Xiling called for the government to give policy support to calcium chloride, an environmentally friendly, resource-intensive product.
According to Wang Xiling, the Soda Ash Association has been promoting dry-ash technology to effectively reduce emissions. Originally in the waste distillation section, lime milk (lime plus water) must be added to steam the ammonia back to the system for reuse. This part of the water increases the discharge of waste liquid. The promotion of dry liming technology, that is, lime into a very fine powder and then added to the system, corresponding to reduce the waste discharge of 20%. After being used in enterprises such as Qingdao Alkali Industry Company and Jiangsu Jingshen Huai'an Soda Plant, the effect is very good. Currently, it is being promoted to ammonia-alkali enterprises.
As we all know, the quality of raw materials will also affect the treatment of waste liquids. For this reason, the Soda Ash Association is implementing a "fine material policy" in companies to reduce impurities in raw materials. As far as the soda industry is concerned, there are few impurities in the well mineral salt and there are many impurities in the sea salt. “As a result, we recommend that companies that use sea salt as a raw material must first wash the salt to remove impurities such as sediment and then put it into the system; in addition, the choice of limestone and coal quality must be strengthened so that emission reductions can be achieved from the source.†Wang Xiling Say.
According to the reporter, in addition to the above-mentioned practices, the use of ammonia-alkali waste slag to remove boiler flue gas is one of the important measures for the reduction and comprehensive utilization of soda ash industry. At present, Guangdong Southern Soda Plant, Qingdao Alkali Industry Company and other companies are applying this technology, both recycling * yellow, but also to find the use of waste residue.
Unlike the ammonia-alkali enterprises whose emission reduction pressures are relatively concentrated, Petronas, Alkali-base and ammonia-alkali enterprises are all faced with more energy-saving pressures. How to further reduce energy consumption has become the common goal of the industry for the next three years after the "Twelfth Five-Year Plan."
“Energy consumption accounts for a relatively large proportion of the total cost of soda ash business. Therefore, we are promoting the use of energy-saving technologies and equipment such as multi-stage steam utilization, heat pumps, and belt vacuum filtration machines in the whole industry. We are also preparing to actively promote automatic control through various meetings. As an important task in the 'Twelfth Five-Year Plan' period after the 12th Five-Year Plan, Wang Xiling told reporters.
Wang Xiling pointed out that multi-stage steam utilization requires that the company's new boiler should be under 100 kg pressure so that the high-pressure steam can be used several times in stages to achieve the purpose of saving the standard coal. At the same time, it is recommended to use the imported heat pump equipment to achieve low-level heat energy. Make full use of.
In addition, the industry has previously commonly used a vacuum drum filter alkaline machine, while the benefits of the belt vacuum filter base is being promoted is: on the one hand to reduce the heavy alkali water, in the calcination section can save a lot of steam; on the other hand, can Reducing the washing water equivalent can save a lot of steam in the distillation section for ammonia companies and reduce the discharge of waste liquid. After the shrinkage of the mother liquor of Lianhua Enterprise, the wastewater discharged by other devices can also be added to the mother liquor system. The “zero discharge†is basically achieved. The lower-moisture heavy alkali can be further calcined to further save steam.
According to Wang Xiling, not only some applicable new technologies play an important role in the energy-saving and emission reduction of the soda industry, but the adoption of automatic control is more conducive to the realization of energy-saving emission reduction targets. In the coming years, regardless of the conference, the association will actively promote this. In May of this year, the association centralized the chief engineer of the system-wide enterprise to Hangzhou. The Zhejiang Zhongguan company did a training to improve the level of automatic control in the entire industry.
“Compared with foreign countries, the whole industry still lacks in automatic control. At present, there is only a control room in each major section, but there is no centralized control. Through training and publicity, we will guide enterprises from centralized control to the whole plant. Concentrate control and move forward." Wang Xiling said.
Plane ruled gratings are characterized by a superior efficiency at their design wavelength compared with holographic gratings. Plane Ruled gratings comprise the majority of diffraction gratings used in spectroscopic instrumentation and are especially useful in systems requiring high resolution.
China star optics can provide customers with a variety of replicated grating products such as diffraction gratings, reflective gratings,holographic gratings,concave gratings etc. to meet different needs. Maximum ruled area is up to 300 x 300 mm for plane ruled diffraction gratings. For replicated diffraction and transmission gratings the ruling density can be from 20 grooves per millimeter to 2400 grooves per millimeter, wavelength from 0.2 micron to 25 microns.
Holographic gratings:
Specifications:
Ruled area: <=70 * 70mm
Wavelength range: 0.2-0.8um
Grooves per mm: 1,200 to 3,600L/mm
Diffraction: >70%
Ruled gratings:
Specifications:
Ruled area: <=70 * 70mm
Wavelength range: 0.2-15um
Grooves per mm: 50 to 2,400L/mm
Diffraction: >70%
Concave gratings:
Specifications:
Ruled area: <=70 * 70mm
Wavelength range: 200 to 900um
Grooves per mm: 490 to 1,200L/mm
Diffraction: >70%
Plane Ruled Grating,Plane Ruled Diffraction Grating,Plane Reflection Grating,Plane Ruled Reflective Grating
China Star Optics Technology Co.,Ltd. , https://www.csoptlens.com