Metal Matrix Composites (MMC) have excellent comprehensive properties such as high specific strength and specific modulus, high temperature resistance, wear resistance and small thermal expansion coefficient. Metal-based composite materials are used instead of steel, aluminum alloy or titanium alloy materials. It can significantly reduce weight, increase speed, improve fuel efficiency, reduce exhaust emissions, reduce manufacturing and maintenance costs, and improve the structural and processability of components. In recent years, aero-engine turbine blades, aircraft wings, landing gear, missile tails Application requirements for housings, inertial navigation platforms, electronic packaging, automotive parts, etc. are very urgent [1-2].
Aluminum matrix composites are typical metal matrix composites and are mainly classified into continuous fiber reinforced aluminum matrix composites and particle reinforced aluminum metal matrix composites. In recent years, particle reinforced aluminum matrix composites have solved the problems of complicated preparation process, immature process and high cost of continuous fiber reinforced metal matrix composites, and the production cost has been greatly reduced. Internationally, attention has been gradually shifted to particle reinforced aluminum matrix composites. In the study of materials, countries have gradually increased their demand.
Although the comprehensive properties of the particle reinforced aluminum matrix composite are superior, its low plasticity, microscopic inhomogeneity and the addition of the superhard ceramic reinforcing phase make it difficult to cut. In order to minimize the machining allowance of aluminum-based composite materials, the researchers tried to manufacture aluminum-based composite parts by the near-net forming method, but in many cases, the parts requirements could not be met, so it is necessary to metal-based composite materials. Carry out systematic cutting process research. Since 1985, Burn et al. [3] published the first paper on the cutting of aluminum-based composite materials, it has been nearly 30 years since the domestic and foreign scholars have carried out a lot of experimental research on the cutting of particle reinforced aluminum matrix composites. . Aluminum-based composite materials mainly have problems such as short tool durability, poor surface quality, low production efficiency, and high processing cost in the cutting process [4-5]. How to carry out high-efficiency and low-cost high-speed cutting has become a research hotspot.
Tool material selection and adaptability
In the machining of particle reinforced aluminum matrix composites, since the hardness of the reinforcing phase is usually higher than that of high speed steel, even higher than that of cemented carbide and some ceramic coated tools, the tool wear rate is extremely high when cutting the material. Domestic and foreign scholars have used a variety of material tools to carry out a large number of cutting experiments on particle reinforced aluminum matrix composites. The results show that PCD cutters have become a cutting aluminum base due to their high hardness, wear resistance and low chemical affinity. Preferred tool material for composite materials [5-12]. Carbide tools have higher tool wear rates during cutting of aluminum-based composites. For example, when cutting aluminum-based composites at higher cutting speeds (v>350 m/min), carbide tools are in tens of seconds. That is, the failure is declared [13-14]. It is generally believed that the cutting speed of such tools when cutting aluminum-based composite materials should be limited to 300m/min [15-22]. Xu et al. [23] studied the machinability of two typical aluminum-based composites using fine-grained carbide, ceramic, CBN and PCD cutting tools, and found that the processing of hybrid reinforced aluminum matrix composites When PCD cutters have the highest wear resistance, they are ideal materials for finishing. When processing fiber-reinforced aluminum matrix composites, the fine-grained carbide tools have low wear rate, good surface integrity and lowest processing cost. The best tool materials for processing different metal matrix composites. Tomac et al. [14] conducted cutting experiments on TiN, TiCN and Al2O3 coated tools prepared by chemical vapor deposition. The results show that TiN coated tools have the best tool life. Manna and Bhattacharya [15] use a stable built-up edge formed during the cutting process to protect the tool to increase the life of the carbide tool. The flank wear rate of chemical vapor deposition (CVD) diamond coated tools is higher than that of PCD tools [6]. D Errico et al. found that increasing the coating thickness of CVD diamond tools can improve the cutting performance. The coating is 500μm thick CVD diamond. The tool is comparable to the PCD [6, 24]. Compared to high-speed steel, TiN coatings, and carbide tools, CBN and PCD tools exhibit better flexibility when cutting particle-reinforced aluminum-based composites. CBN can be used as a replacement tool for PCD under certain conditions [25] ], but Ibrahim Ciftc [26] showed that when cutting SiCp/Al composites with a silicon carbide particle size of 110 μm, the cutting edges and tips of CBN tools are severely damaged. Under these conditions, CBN tools are not suitable for cutting. Under normal conditions, PCD has better wear resistance, higher breaking strength and lower adhesion than PCBN, which shows better cutting performance than PCBN tools [12].
In order to improve surface roughness and reduce subsurface damage, PCD has better applicability in various tool materials for high speed cutting of particle reinforced aluminum matrix composites, thus becoming the preferred tool material [9,12,27-28 ].
Cutting force and cutting temperature
The results of Xu et al. [23] show that the cutting force increases with the increase of cutting speed when cutting four kinds of tool materials. Manna et al. [15] used uncoated cemented carbide for dry turning test of vol.15%SiCp/Al in the range of cutting speed v=20~225m/min. The results show that the main cutting force increases with the cutting speed. The decrease (from 220N to 135N) increases with increasing feed rate and depth of cut (from 125N to 170N). El-Gallab [5] and other studies have found that the cutting force decreases with the increase of cutting speed and depth of cut. It is believed that the softening of the workpiece material and the existence of built-up edge can change the geometry of the tool. Lin et al. [9] used a PCD tool to perform a turning test on SiCp/Al at cutting speeds of v=300, 500, and 700 m/min, respectively. The results show that with the increase of tool wear, the main cutting force and feed resistance are within 185N and 90N respectively; under the same cutting speed, the cutting force increases with the increase of feed rate; under the same feed condition, The cutting force changes little with increasing cutting speed. Pramanik et al. [29] established a mechanical model for predicting the cutting of aluminum-based composites based on the McCent model. It is believed that the forces in the cutting process come from three aspects: chip deformation force, plough force and particle crushing force. El-Gallab, Sklad [10] established a practical 3D tool model for predicting the stress, temperature and wear of the tool when cutting SiCp/Al; the results show that the highest cutting temperature is on the cutting edge and along the rake face temperature Gradually lowering, the cutting temperature is increased with the feed rate; due to the higher thermal conductivity of the PCD, the cutting temperature of the PCD tool is lower than that of the TiN, Al2O3 tool. Chou and Liu [30] cut SiCp/Al with CVD diamond coated tool, measured the cutting temperature under different cutting conditions, and found that cutting speed is the main factor affecting cutting temperature, and verified by ANSYS, and the test results were obtained. Better consistency. Bian Weiliang et al. [31] established a cutting force prediction model for high-speed milling of SiCp/2009Al composites with PCD tools based on factors such as milling speed, feed per tooth, radial width and enhancement of phase ratio. The model has a high prediction accuracy for milling forces.
Lu Jiechi et al. [32] used the embedded thermocouple method to test the SiCp/Al composites, studied the influence of cutting parameters on the front and back flank, and compared the four cooling conditions (dry cutting, Cutting temperature under compressed air air cooling, oil casting and MQL). Under the four conditions, the tool temperature from high to low is dry cut, air cooled, oil cooled, MQL, and the rake face temperature is lower than the flank face under dry cutting conditions. Ge Yingfei et al [33-34] studied the cutting force and cutting temperature with PCD tool high-speed milling SiCp/2009Al composite material. The dynamic milling force at the initial stage of tool wear, the peak value of radial force Fy has exceeded 1300N, and the cutting vibration is severe. . Studies have shown that the cutting force decreases with the increase of the cutting speed, and the cutting force increases with the increase of the feed rate or the depth of cut; the height of the enhanced phase ratio and the size of the small enhancement phase are higher. Large cutting force; T6 heat treatment can significantly increase the cutting force; using cutting fluid can greatly reduce the cutting force. Studies have shown that milling temperatures can reach above 580 ° C. Cutting parameters, tool materials, workpiece materials and tool wear conditions have a significant effect on the cutting temperature, while tool geometry has a small effect. The order of influence of cutting parameters on cutting temperature is: cutting speed, enhanced particle body ratio, radial cutting width, and feed per tooth. With cutting parameters, enhanced particle fraction/size, PCD grain size and tool wear increased, the cutting temperature increased significantly. Under the same cutting parameters, the cutting temperature is significantly reduced when milling T6 heat treated aluminum matrix composites at high speed.
Tool wear and tool durability
Li Dan et al. [35] used K10 cemented carbide milling cutter to perform medium-high speed (1000~1800r/min) milling of Al2024/SiCp composite under dry conditions. The test shows that the failure mode of the tool during machining is mainly the back knife. There are two forms of surface wear and chipping, and the enhanced particle size has an important influence on the failure mode of the tool.
Ge Yingfei et al [36-37] high-speed milling of SiCp/Al composites using PCD tools, the results show that the high-frequency scribe and impact of reinforced silicon carbide is the abrasive wear (Fig. (a)), the cutter grains fall off (Fig. (b)), the main mechanism of chipping (Fig. (c)) and spalling (Fig. (d)). PCD tool base microcracks (Fig. (e)) are produced by cutting high volume fraction workpiece materials, heat treated composites or using high cutting speeds to enhance particle impact, cutting vibration and thermal shock. The continuous generation and shedding of the built-up edge during dry cutting causes the tool to wear and wear (Fig. (f), (g)). The aluminum and copper elements in the workpiece material diffuse to some extent in the tool. The tool experienced slight graphitization wear (Fig. (h), (i)). Reinforced particle volume fraction is the most significant factor affecting tool wear. Enhanced particle size, heat treatment of workpiece materials, tool material grain size and cooling conditions have a significant impact on tool wear. The cutting speed has the most significant influence on the tool durability in the cutting parameters, and the feed per tooth is second. The roughness and quality of the machined surface are significantly sensitive to tool wear.
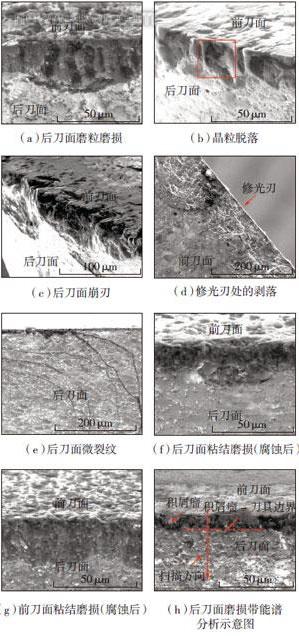
Ge Yingfei and other researches have also shown that the tool durability of PCD tools for high-speed cutting of SiCp/Al composites exceeds 150 min (sharp standard VB = 0.1 mm), while the wear of the carbide tool after cutting for 3 min exceeds 0.35 mm.
Lin et al. [9] found that the tool durability of PCD tools decreased with increasing cutting speed and feed rate. D'Errico et al. [24] used PCD and CVD tools to perform a comparison test of 359/SiC/20p composites at a cutting speed of v=500 m/min and found that when the feed rate is small (0.1 mm/r), the thickness is thick. The tool durability of the film CVD (500μm) tool and PCD tool is 600min and 950min respectively, but the tool durability of the thick film (500μm) CVD tool and PCD tool is 32min when the feed rate is increased to 0.4mm/r. And 1080min, the results show that as the feed rate increases, the tool durability of thick film CVD tools drops sharply, while the tool durability of PCD tools does not change much.
Research on chip formation mechanism of high speed cutting
Pramanik et al. [38] studied the chip morphology of SiCp/Al composites at a cutting speed of v=400 m/min and found that the chips were short and irregular when the feed was 0.025 mm/r, with the feed rate. The increase (0.05~0.1mm/r), the chips become longer and spiral and linear, and the feed rate is further increased (0.2~0.4mm/r), and the chips become shorter and C-shaped. However, when the aluminum alloy is cut, the shape of the chip does not change significantly as the feed amount or the cutting speed increases. Nodular and discontinuous chips are the most common chip form for cutting aluminum-based composites [38-39].
Quan Yanming et al [40] studied the chip forming mechanism of hard and brittle granular reinforced metal composites, and found that the aluminum matrix entrapped particles have non-directional continuous slip after shearing into the shear deformation zone, shearing along the shear plane, and basically stable. Sliding 3 variants. In addition, the shear angle cannot be budgeted by the general analytical method, and the empirical value can only be obtained through experiments.
Ge Yingfei et al. [41] studied the chip formation mechanism of SiCp/Al composites during high-speed milling. The results show that the chips are generally irregular zigzag discontinuous (Fig. (a)), and the free surface of the chips has aperiodic Sexual shear cracks extend into the interior of the chip (Fig. (b)), and a large number of microvoids and microcracks are present in the first shear zone (Fig. (c)) and the chip (Fig. (d)). These microvoids and microcracks are mostly formed around the reinforcing particles, and a few are formed in the aluminum matrix, and their directions are substantially consistent with the direction of material deformation (Fig. (d)). Studies have shown that the formation and expansion of microvoids and microcracks have an important influence on the chip formation process of SiCp/Al composites. The study also shows that the shear angle of SiCp/Al composites during the formation of chips is not constant, and there is a tendency to have a zigzag shape. When cutting SiCp/Al composites, the shear deformation zone matrix is ​​always wrapped with broken silicon carbide particles for uneven coordinated deformation (particle rotation), slip (including a large number of grain boundaries, slip between phase boundaries) The direction of shifting often changes. Since the SiCp/Al composite matrix used in the test has good plasticity, small silicon carbide particles and low volume fraction, the slip of the aluminum matrix in the shear deformation zone is similar to that of non-reinforced metal, and it can continuously and stably align the slip. However, the matrix near the particles still has a small amount of uneven deformation, which makes the deformation flow line of the material unclear (Fig. (c)). Nevertheless, the reinforcing particles have a tendency to flow in the direction of shear deformation of the material (Fig. (e)). The results show that the SiCp/Al composites have a non-uniform sawtooth shape, and the volume fraction of the particles and the heat treatment state of the workpiece have a significant effect on the chip formation. The dynamic formation and expansion of the pores and microcracks are the main mechanisms of chip formation. The chip formation process is also accompanied by a certain degree of adiabatic shear.
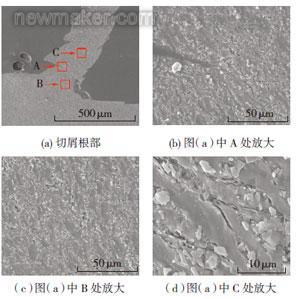
Surface integrity study
Pramanik et al. [38] performed a comparative test on the SiCp/6061Al composite and 6061Al alloy. It was found that the surface roughness of 6061Al is higher than that of SiCp/6061Al at low feed rate, but it occurs when the feed rate is greater than 0.03mm/r. Change. The surface roughness of 6061Al is higher than that of SiCp/6061Al in the range of cutting speeds tested. No indentation marks were found on the machined surface of the composite material, and the cutting speed had no significant effect on the surface roughness of the machined surface.
The study by El-Gallb et al. [42] shows that when cutting SiCp/Al composites, the machined surface has voids around the silicon carbide particles and is accompanied by the extraction, fracture and fracture of the particles. The machined surface is dragged to cause scratches to form grooves, and the machined surface roughness decreases as the feed rate increases, and the negative front angle results in a large surface roughness.
Wu Zhenyu et al. [43] high-speed milling of SiCp/Al composites using TiAlN coated tools. The results show that the increase of milling speed results in a significant increase in vibration, a significant increase in surface defects and a significant increase in surface roughness.
Ge et al. [44] studied the high-speed milling of SiCp/Al composites using PCD tools, which showed that the surface roughness increased significantly with the increase of the blade wear. In the initial wear stage of the tool, the surface roughness of the SiCp/Al composite is low (Ra is about 0.207 μm). Among the factors affecting the surface roughness, the volume fraction of the reinforcing phase has the greatest influence, and the cutting speed is second. The speed is the smallest.
Ge Yingfei et al. [41] have shown that the high-speed milling of aluminum-based composites has a machined surface consisting mainly of cutting ripples generated by tool cycle feed, as well as potholes, microcracks, matrix tears, and coatings generated during particle removal. Non-tools such as covers and protrusions directly cut out the elements. During high-speed cutting, due to the large cutting force and high cutting temperature, the workpiece material at the tip of the tool significantly expands plastically and plastically flows along both sides of the tool tip. Due to uneven material deformation during high-speed cutting, the shear angle fluctuates within a certain range, resulting in unstable cutting and obvious vibration lines on the machined surface.
Studies have also shown that the amount of cutting, the particle size ratio/size of the granules, the grain size of the tool material, the cooling method, and the heat treatment state of the workpiece all have a significant effect on the surface formation. When cutting higher-merity composite materials, the machined surface contains more constituent elements such as micro-pits, microcracks, and matrix tears. At higher cutting speeds, the situation in which the reinforcing particles are severed or pressed in place is significantly increased. When cutting the same body-part composite material, the larger the reinforcing particle size, the larger and deeper the pits remaining on the machined surface, and the more severe the tearing and vibration of the substrate. When using the coolant, the chips and debris are carried away by the coolant under the action of the rinsing action and the large centrifugal force, so that the chance of enhancing the granules or debris being re-pressed into the machined surface by the tool is greatly reduced. When using a smaller-grain PCD tool, the number of pits remaining on the machined surface is reduced because the tool has better sharpening quality and longer tool life.
Ge Yingfei et al [45] found that the depth of the hardened layer of the surface of the unheated material is 30~35μm, while the depth of the hardened layer of the surface of the heat treated material is 15~20μm. The highest value of work hardening is 10~15μm away from the machined surface.
Conclusion
In summary, research on high-speed cutting of aluminum-based composites focuses on tool selection, chip morphology, tool wear, surface integrity, cutting force and cutting temperature. Numerous studies have shown that high-speed cutting of aluminum-based composites with PCD tools results in better surface quality, higher tool life and lower cutting forces and cutting temperatures.
In recent years, high-speed, high-efficiency and precision cutting of metal-based composite materials have received widespread attention. However, there are mutually independent and even contradictory conclusions between the conclusions of many related studies. The application value of engineering is limited, and the tool life modeling needs to be increased. Research on surface roughness prediction, cutting parameter optimization, high-speed milling database and expert systems. PCD cutting tools for high-speed cutting of aluminum-based composite materials can effectively improve the surface quality, material removal rate and processing cost. However, the mechanism of PCD cutting tools for high-speed cutting of aluminum-based composite materials is not clear, and further research is needed. In addition, the current research on high-speed cutting of metal matrix composites is limited to aluminum-based composite materials. Research on the newly developed titanium-based composite materials has not been reported, as the material is expected to replace titanium alloys in the field of aero-engines or Nickel-based superalloys are particularly important and urgent for their research on high-speed machining and mechanism.
Concerned about surprises
Tag: Aluminum Matrix Composites High Speed ​​Cutting Cutting Speed ​​Cutting Force Tool Material
Previous: Heat-resistant conveyor belt maintenance determines life Next: Target flowmeter causes error and solution
China Compression Springs Stainless Steel Compression Spring
Compression Springs,Heavy Duty Compression Springs,Stainless Steel Compression Springs,Metal Springs Compression
applicaiton: viation,automotive, motorbike, bicycle, automatic equipment, household appliance, medical device ,toy, telecommunication,computer, instrument and meter,furniture, electric tools,mold and other industries
China leading manufacturers and suppliers of Compression Springs,coil spring,compress spring coil,Heavy Duty Compression Sprins,Stainless Steel Compression Spring,Metal Compression Spring, etc.
coil spring,compress spring coil,Heavy Duty Compression Sprins,Stainless Steel Compression Spring,Metal Compression Spring
Shenzhen Lanejoy Technology Co.,LTD , https://www.compressionspring.net