Summary: MAG. welding process test on Q235-A and Q345A steels, comparing metal composition and mechanical properties of welds, MAG. welding attempts on the loader cab based on process test and from process performance, mechanical properties, cost Contrast, further explain the promotion of MAG. Welding has a very broad application prospects.
1 Characteristics of two types of gas shielded welding a. Carbon dioxide gas shielded welding. The arc stability is poor, the droplets are non-axially transitioned, the splash is large, the weld formation is poor, the transition coefficient of the wire alloy is reduced (about 8% ¬ 12%, the wire is wasted as a splash after melting), and the weld metal has low impact toughness. Wait.
b. MAG welding (Ar + carbon dioxide mixed gas shielded welding). The arc stability is remarkably improved, the droplets are refined, the transition frequency is increased, the splash is greatly reduced (the spatter rate is 1% to 3%, and there is almost no splash when the jet transition is used), and the weld bead is beautifully formed. In addition, the use of mixed gas protection can also improve the shape of the penetration, the defects such as incomplete penetration and cracking are greatly reduced, and the weld metal properties can be improved, the post-weld cleaning workload can be reduced, the energy consumption can be reduced, and the operating environment can be improved.
2 Process test 2.1 Test materials and equipment Test materials are commonly used welding materials for construction machinery: Q345A, Q235-A; wire type and specification: ER50-6, & 1.2; protective gas: bottled carbon dioxide gas, bottled 80% Ar + 20% carbon dioxide mixed gas Welding equipment: NBC-500 carbon dioxide gas shielded welder; the test plate size is 350mm × 250mm × 16mm, as shown in Figure 1.
2.12 Test method The Q345A and Q235-A test plates were welded by MAG welding and carbon dioxide welding respectively. The welds with grooved side welds were welded in 3 layers, and the back side was cleaned with carbon arc gouging for 3-4 mm. One layer, welding specifications are shown in Table 1, and the test results are shown in Table 2 and Table 3.
2.3 Test conclusions a. Mixed gas shielded welding eliminates the narrow and deep welds of carbon dioxide welds in the form of weld pools, reducing the tendency of welds to be unfused and cracked.
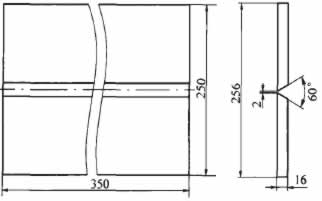
Figure 1 Test board size chart
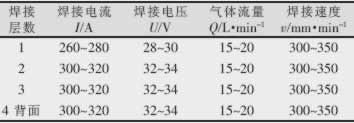
Table 1 Welding specifications

Table 2 % of deposited metal chemical composition
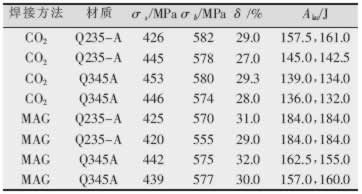
Table 3 Experimental study on mechanical properties of deposited metal
b. The welding spatter is greatly reduced, and there is almost no splash when using the jet transition, which improves the utilization of the welding consumables and reduces the cleaning of the spatter.
c. The surface of the weld is smooth and beautifully formed. The weld slag shrinks into a lenticular shape on the surface of the weld, which is easy to remove and reduces the amount of weld grinding work.
d. The content of Si and Mn in the weld metal is higher than that in the case of carbon dioxide welding. The impurity elements of S, P and Cu are basically similar, and the C content is reduced, that is, the burning loss of Si and Mn elements is 31% lower than that of carbon dioxide welding. -34%, the decarburization rate was 17.6% due to the reduction of carbon in the protective atmosphere.
e. The yield strength and tensile properties of the deposited metal are slightly lower than those of the carbon dioxide welding, and the elongation and impact work are greatly improved, that is, the comprehensive performance is improved.
3 The application of mixed gas is based on the process test. The MAG welding process is applied on the cab with strict appearance quality requirements. Table 4, Table 5 and Table 6 respectively have two kinds of process performance, mechanical properties and welding cost. The welding method is compared.
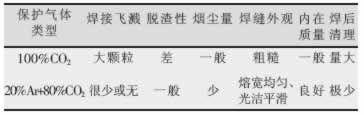
Table 4 Process performance and welding quality
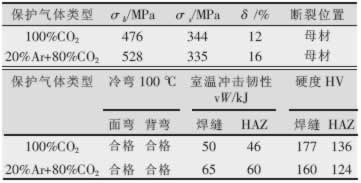
Table 5 Mechanical properties of welded joints
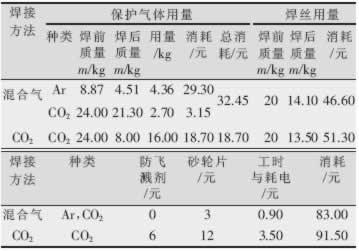
Table 6 welding a cab consumables comparison table
4 Conclusion a. MAG welding process performance is better than carbon dioxide welding, carbon dioxide gas shielded welding machine is suitable for MAG welding, in the engineering machinery industry that has popularized carbon dioxide gas shielded welding, it is easier to promote this process.
b. Compared with carbon dioxide gas shielded welding, MAG welding seams are well formed and splashes are greatly reduced. The overall performance of weld metal is better than that of carbon dioxide gas shielded welding, and the welding cost is close.
c. Using MAG welding can reduce the repair rate of welds, save energy and welding materials, improve welding quality, reduce the labor intensity of workers, improve the operating environment, and have better comprehensive benefits, which is worthy of popularization and application.
1 Characteristics of two types of gas shielded welding a. Carbon dioxide gas shielded welding. The arc stability is poor, the droplets are non-axially transitioned, the splash is large, the weld formation is poor, the transition coefficient of the wire alloy is reduced (about 8% ¬ 12%, the wire is wasted as a splash after melting), and the weld metal has low impact toughness. Wait.
b. MAG welding (Ar + carbon dioxide mixed gas shielded welding). The arc stability is remarkably improved, the droplets are refined, the transition frequency is increased, the splash is greatly reduced (the spatter rate is 1% to 3%, and there is almost no splash when the jet transition is used), and the weld bead is beautifully formed. In addition, the use of mixed gas protection can also improve the shape of the penetration, the defects such as incomplete penetration and cracking are greatly reduced, and the weld metal properties can be improved, the post-weld cleaning workload can be reduced, the energy consumption can be reduced, and the operating environment can be improved.
2 Process test 2.1 Test materials and equipment Test materials are commonly used welding materials for construction machinery: Q345A, Q235-A; wire type and specification: ER50-6, & 1.2; protective gas: bottled carbon dioxide gas, bottled 80% Ar + 20% carbon dioxide mixed gas Welding equipment: NBC-500 carbon dioxide gas shielded welder; the test plate size is 350mm × 250mm × 16mm, as shown in Figure 1.
2.12 Test method The Q345A and Q235-A test plates were welded by MAG welding and carbon dioxide welding respectively. The welds with grooved side welds were welded in 3 layers, and the back side was cleaned with carbon arc gouging for 3-4 mm. One layer, welding specifications are shown in Table 1, and the test results are shown in Table 2 and Table 3.
2.3 Test conclusions a. Mixed gas shielded welding eliminates the narrow and deep welds of carbon dioxide welds in the form of weld pools, reducing the tendency of welds to be unfused and cracked.
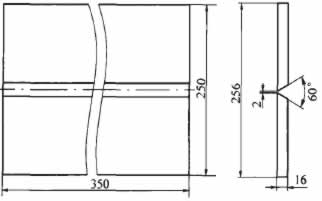
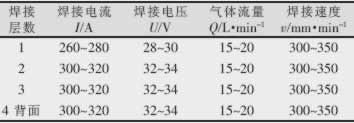

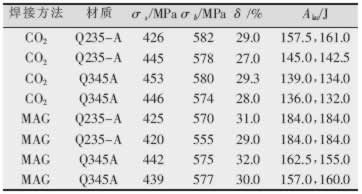
b. The welding spatter is greatly reduced, and there is almost no splash when using the jet transition, which improves the utilization of the welding consumables and reduces the cleaning of the spatter.
c. The surface of the weld is smooth and beautifully formed. The weld slag shrinks into a lenticular shape on the surface of the weld, which is easy to remove and reduces the amount of weld grinding work.
d. The content of Si and Mn in the weld metal is higher than that in the case of carbon dioxide welding. The impurity elements of S, P and Cu are basically similar, and the C content is reduced, that is, the burning loss of Si and Mn elements is 31% lower than that of carbon dioxide welding. -34%, the decarburization rate was 17.6% due to the reduction of carbon in the protective atmosphere.
e. The yield strength and tensile properties of the deposited metal are slightly lower than those of the carbon dioxide welding, and the elongation and impact work are greatly improved, that is, the comprehensive performance is improved.
3 The application of mixed gas is based on the process test. The MAG welding process is applied on the cab with strict appearance quality requirements. Table 4, Table 5 and Table 6 respectively have two kinds of process performance, mechanical properties and welding cost. The welding method is compared.
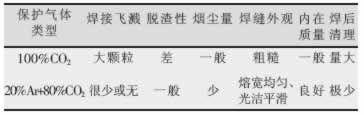
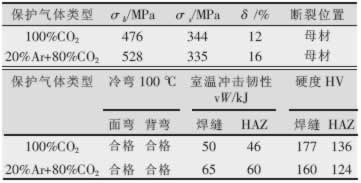
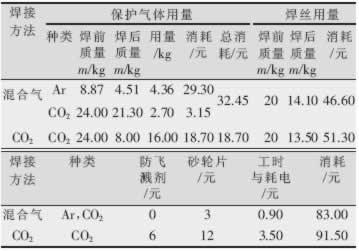
4 Conclusion a. MAG welding process performance is better than carbon dioxide welding, carbon dioxide gas shielded welding machine is suitable for MAG welding, in the engineering machinery industry that has popularized carbon dioxide gas shielded welding, it is easier to promote this process.
b. Compared with carbon dioxide gas shielded welding, MAG welding seams are well formed and splashes are greatly reduced. The overall performance of weld metal is better than that of carbon dioxide gas shielded welding, and the welding cost is close.
c. Using MAG welding can reduce the repair rate of welds, save energy and welding materials, improve welding quality, reduce the labor intensity of workers, improve the operating environment, and have better comprehensive benefits, which is worthy of popularization and application.
HSS DRILL BITS ARE USED IN DRILLING HOLES ON STEEL MATERIAL.
2Mm Drill Bit,11Mm Drill Bit,High Speed Drill,High Speed Steel Drill Bits
DANYANG TRUST IMPORT & EXPORT COMPANY LIMITED , https://www.dytrust-tools.com