One: coal quality test method / coal quality test knowledge / coal test equipment technical questions and answers
1. What is the meaning of volatiles? What are the technical requirements for the determination of volatiles?
Answer: The volatile matter of coal refers to the product of gas and liquid (in the state of steam) which is decomposed by organic matter in coal by heating the coal sample at 900±10 °C for 7 min .
The determination of volatile matter is a highly regulated test, and the results of the measurement are completely dependent on the specified test conditions. Therefore, when determining the volatile matter of coal combustion, the technical requirements for the measurement are very strict. details as follows:
Technical requirements: ( 1 ) The temperature inside the high temperature furnace should be strictly controlled within the range of 900±10 °C . When the sample is placed, the furnace temperature should be restored to 900±10 °C within 5 minutes .
( 2 ) The timing of the heating time is applied to the stopwatch, that is, when the sample is sent to the high temperature zone of the high temperature furnace to start timing, until the sample leaves the high temperature furnace, the operation process should be accurate for 7 minutes . Otherwise, the sample is discarded.
( 3 ) Apply a dedicated crucible for the measurement. When the crucible is burning in the furnace, direct contact between the crucible and the crucible and the high temperature furnace wall should be avoided.
( 4 ) At the time of measurement, if black smoke is collected on the lid of the crucible or the crucible, the test is also scrapped.
2. What should you pay special attention to when measuring three-stage furnaces? Explain the principle and equipment?
Answer: Principle: The first electric furnace plays the role of heating and burning the sample, the second electric furnace is used to burn the unoxidized product after the oxidation test pyrolysis, and the third electric furnace is used to supplement the combustion process, and is carried out under closed oxygen. .
Equipment: porcelain boat, grinding plug, with foot glass tube.
The notes are as follows:
( 1 ) During the combustion process, the conditions for complete combustion of the sample must be met. No matter how much reaction is experienced during the combustion process, the carbon and hydrogen in the sample can be quantitatively converted into carbon dioxide and water.
( 2 ) The product of the interference reaction must be removed so that only pure carbon dioxide and water enter the absorption device after the combustion reaction.
( 3 ) It is necessary to select an appropriate absorbent so that carbon dioxide and water can be absorbed quantitatively; at the same time, a certain gas flow rate is maintained, so that the absorption reaction can be carried out for a sufficient period of time, and the gas flow rate is also a necessary condition for ensuring complete combustion.
3. What are the elements of carbon and hydrogen interference measurement? How to exclude?
A: combustion of SO2, NO2, Cl2 will interfere with the determination, to exclude formation of PbSO4 and SO2 at 600 deg.] C under the action of its use PbSO4 Be Removed, Cl2 metal? Silver and its role in the production of about 200 ℃ AgCl is removed, and metallic silver can be SO2 ?? deg.] C under conditions of higher than 500 It is removed by formation of Ag2SO4 , and NO2 is removed by the action of granular MnO2 to form Mn ( NO3 ) 2 .
4. What should be noted when using the aldrin method to determine total sulfur in coal?
A: When using the aldrin method to determine total sulfur in coal, the following issues should be noted:
( 1 ) Semi-melting must be carried out under ventilation, otherwise the combustion of the coal particles is incomplete and some of the sulfur cannot be converted into sulfur dioxide;
( 2 ) The precipitant BaCl2 must be in excess;
( 3 ) When extracting and washing with water, the volume of the solution should not be too large, so as not to affect the measurement results;
( 4 ) Pay attention to adjusting the acidity of the solution to convert CO32- to CO2 ;
( 5 ) In the washing process, the washing liquid should be drained before each inhalation of distilled water, so that the washing effect is good;
( 6 ) Filter paper should not be left before burning, and the high temperature furnace should also be ventilated;
( 7 ) After the burned BaSO4 is cooled in the dryer, it is weighed in time;
( 8 ) A blank test must be done.
5. What is the meaning of fuel coal calorific value?
Answer: The calorific value of fuel refers to the amount of heat released per unit weight of fuel when it is completely burned. The unit is J/g or MJ/kg .
What are the requirements for the coal calorimetry chamber?
Answer: ( 1 ) The heat chamber should be used as a special room for measuring calorific value, and no other test work should be carried out indoors;
( 2 ) The room should be equipped with curtains to avoid direct sunlight;
( 3 ) It is advisable that the temperature change does not exceed 1 °C for each measurement ; the difference between room temperature in winter and summer is not more than 15~30 °C . Therefore, those who are qualified should prepare air conditioning equipment;
( 4 ) When measuring the calorific value, strong ventilation and heat source radiation should be avoided indoors. In short, in order to reduce the influence of environmental conditions on the calorific value measurement results, the calorific value measuring chamber should be kept as relatively constant as possible at room temperature. The calorific value shall not be measured when the room temperature is not constant.
6. What should I pay attention to during the oxygen bomb oxygenation operation?
Answer: ( 1 ) First check whether the oxygen pressure gauge is intact and sensitive, whether the indicated pressure is correct, and whether the operation is safe.
( 2 ) When the oxygen bomb is oxygenated, the pressure must be slowly increased until the specified pressure is maintained for 0.5-1 min .
( 3 ) Do not touch grease when using oxygen.
( 4 ) Oxygen bomb oxygenation should be carried out according to the specified pressure, and the oxygenation pressure should not be too low or too high.
7. After a calorific value measurement, it was found that there was an unburned coal sample in the combustion vessel. What is the reason for the test?
A: The possible reasons are:
( 1 ) insufficient oxygenation pressure or oxygen bomb leakage;
( 2 ) The coal quality is too poor and the volatile matter is too low;
( 3 ) The oxygenation rate is too fast or the position of the combustion vessel is not correct, so that the sample is splashed;
( 4 ) The ignition wire is buried deep in pulverized coal;
( 5 ) The sample has too much water content or the coal powder is too thick.
8. What is the reason for not burning in the burning dish?
A: The reason is:
( 1 ) Poor contact of the ignition switch or adjustment knob;
( 2 ) the ignition wire and the electrode fall off;
( 3 ) the ignition wire is in contact with the combustion vessel or the combustion vessel in contact with the other electrode to cause a short circuit;
( 4 ) The ignition wire is in poor contact with the sample;
( 5 ) The oxygenation pressure is low;
( 6 ) The moisture content of the sample is too high, the volatile content is too low, and the sample particles are too large;
( 7 ) The oxygen bomb leaks.
9. What are the precautions for using the balance? how to use?
A: Use: Any balance must be zeroed first (some balances should be level). It can then be weighed. The weight must be returned after use. There must be a power outage when there is power.
Note: ( 1 ) The same balance must be used in the measurement of the same sample, the same set of weights;
( 2 ) During the weighing process measured in the same sample, the zero adjustment shall not be repeated multiple times.
( 3 ) The mass of the object referred to shall not exceed 1/2 of the maximum load of the balance .
( 4 ) It is not possible to weigh objects that are too cold or too hot on the balance.
( 5 ) The object to be weighed shall not be in direct contact with the weighing pan. Deliquescent, volatile materials must be in a covered container, corrosive substances should be placed in a sealed container.
( 6 ) When weighing, the object is placed on the left plate and the weight is placed on the right plate.
( 7 ) When rotating the brake knob, it should be adjusted slowly and evenly, when the balance beam starts or brakes smoothly, if the pointer is still swinging, it should be braked when the pointer is near the center zero point.
( 8 ) When adding or removing items from the scale, when adding a subtraction code or switching the glass door of the balance, the balance must first be braked.
( 9 ) After adding items or adding or subtracting weights, the doors must be completely closed before the balance is read to read the readings.
( 10 ) When adding weights to the plate, they should be in a certain order.
( 11 ) Apply the weight of the tweezers and do not take them by hand.
( 12 ) Each balance has a fixed weight and the entire weight must not be dismantled and used in another balance.
( 13 ) Protect the balance from direct sunlight. Cover the dust cover after using the balance.
( 14 ) The balance should be kept clean and a soft brush or silk cloth should be used to wipe the dust or spilled sample. If there are dirty stains on the parts, wipe them off with a cloth dampened with anhydrous alcohol.
( 15 ) Silicone should be placed in the balance and replaced regularly and dried.
10. What is the standard coal consumption? Calculate the coal consumption of the internship manufacturer. How much do you think the coal consumption of our factory is expected to be controlled? How to calculate? (What data is needed?)
Answer: Coal consumption is the main economic assessment index of thermal power plants. However, the calorific value and total moisture of fuels used in different plants and different boilers of the same plant and even in different stages of the same boiler are different, that is, low fuel emissions. Heat, the effective heat value that is actually available in the fuel is different. In order to adopt a unified standard as the basis for calculating coal consumption, we will receive coal with a base low calorific value of 29271KJ/Kg as standard coal, that is, every 29271KJ/Kg of heat is converted into 1Kg of standard coal. In this way, the coal consumption of various low calorific values ​​is unified to the standard coal consumption.
Standard coal consumption: b = ( Qnet , ar·G ) / ( 29.27E ) ??? unit is Kg / (Kw · h)
Where: G - the weight of the coal (applied coal), Kg
Qnet , ar - low calorific value calculated according to the received base, MJ/Kg
E - power generation, Kw·h
29.271 - calorific value of standard coal, MJ/Kg
Introduction to low volatile coal:
According to the coal quality standard for power generation in China , the dry ashless base Vdaf is less than 20% low-volatile coal , and less than 6.5% is ultra-low volatile coal. The ignition of coal is related to the quality and quantity of volatiles. As the degree of coalification increases , the volatile matter content decreases , and the ratio of the calorific value of the volatiles in the calorific value of the coal decreases , making the ignition of the coal difficult ; the lithofacies structure of the coal also changes , and the deepening of the coalification makes the structure tight. Stable , small porosity , which makes the coal's grinding performance weakened , the reactivity is reduced , and the burnout is deteriorated.
Therefore , low volatile coal is characterized by difficulty in ignition and burnout , requiring high ignition and burnout temperatures , and a long burnout time. Studies have shown that [3], the ignition of anthracite occurs on the particles , the volatiles are precipitated in the further combustion process, and the volatiles have little effect on the fire. Burnout to obtain satisfactory results, must be worn anthracite finer surface area is increased so as to accelerate the ignition and burnout. . In general , Vdaf can roughly determine the difficulty of burning and burning. However, in the long-term study of burning low-volatile coal in China , it is found that even the two coals with the same Vdaf have different combustion characteristics. Therefore , there must be more reliable discriminant data. Studies showed that the ignition temperature of the pulverized coal flow to determine IT fire more precise degree of difficulty, it is easier to fire coal IT deg.] C; IT = 700 ~ 800 ℃ moderate fire coal; IT ≥800 ℃ is difficult to fire coal. Among the many low-volatility coals in China , the most difficult to burn are the Jiafu anthracite coal in Fujian and the Wannian anthracite coal in Hebei . They are all very low volatile coals , Vdaf is about 4% , and the ignition temperature IT is 970 °C. And 1100 °C , it is extremely difficult to catch fire ; the burnout index RJ is 2.94 and 2.32 respectively , which is extremely difficult to burn. Jiafu anthracite is also a medium-sludge coal with low ash melting point.
In order to ensure the stability of fire and combustion , its primary task is to take effective measures to ensure the timely ignition of the pulverized coal gas stream. It is necessary to have a higher furnace flame temperature and sufficient pulverized coal particle residence time , and at the same time , the wind powder must be mixed in a timely and uniform manner in the furnace. For some low-volume coal with low ash melting point , measures should be taken to prevent severe slagging in the furnace under the premise of ensuring stable combustion .
The refractory belt can be laid on the water wall, and the liquid slag can be used. The combustion method of W or U -type flame can be used. For example, DC or swirl can be used by the burner designed by the University of Technology (good combustion effect, an advertisement), improve Fineness of pulverized coal and concentration of pulverized coal in primary airflow.
However, some measures are not conducive to reducing NOx , the tendency to slagging and high temperature corrosion, depending on the specific conditions, the corresponding approach is adopted. But steady combustion should be the first choice.
Two: coal quality analysis technology / coal quality analysis knowledge - coal test technology question and answer
1. What industrial analysis projects are involved in coal combustion in coal quality analysis? What are the element analysis projects? What symbol is used to indicate?
Answer: The non-combustible components and combustible components of coal measured by industrial analysis, the former is moisture and ash, the latter is volatile and fixed carbon, which are represented by M , A , V , and Fc , respectively .
The elemental analysis items are: carbon ( C ), hydrogen ( H ), oxygen ( O ), nitrogen ( N ), sulfur ( S ), moisture ( M ), and ash ( A ).
2. What is the benchmark for coal burning? What kinds of benchmarks are there?
A: In industrial production or scientific research, sometimes some components in coal are removed and recombined for a certain purpose and the composition percentage is calculated. This combination is called a benchmark. There are receiving base, air drying base, dry base, dry ashless base.
3. What is inferior coal? What is the hazard for boiler combustion? why?
Answer: Inferior coal refers to various coal products with high ash content. Low-grade coal is used for boiler combustion. It is not only economically poor, but also causes serious wear of combustion auxiliary system and convection heating surface and increase of maintenance cost, because poor coal ash is compared. High, poor economy, large ash content, serious erosion and wear on the heated surface.
4. How to manually sample the incoming coal?
Answer: The coal entering the coal-fired power plant is mostly sampled in the coal flow of the coal conveying belt. When manually sampling on the coal conveying belt, the shovel should be taken close to the belt once, without leaving the bottom coal. If it is divided into two samples, it should be The rotation is sampled on both sides of the belt, and the two are combined into one subsample. The manual sampling is limited to the belt speed not exceeding 1.5 m / s , the coal seam thickness on the belt is not more than 0.3 m , and the coal transportation amount is not more than 200 T / h .
5. Write the whole process of shrinking coal samples? The purpose of each step? What are the principles?
A: It includes five steps of crushing, sieving, blending, shrinking and drying. When it is necessary to use floating coal for analysis and analysis, it also needs to carry out the ash reduction step: ( 1 ) crushing ? The purpose is to reduce the viscosity and increase the coal particles. degree of dispersion, improved unevenness coal;? (2) screening the coal sample is crushed to the necessary size, to use a variety of screening mesh sieve;? (3) of the coal after blending riffler representative sample without loss, should be blended before each riffling, homogenized, blended coal pile cone method employed;? (4) reduction of sub-samples reduces the coal, without losing its representation; (5 ) Drying ? When the coal sample can pass through the crusher, the shrinking machine, the divider and the sieve smoothly, it cannot adhere to the sieve; ( 6 ) Ash reduction ? For the coal sample to be ash reduced, the raw coal sample is placed in the heavy liquid. Flotation is carried out to achieve the purpose of ash reduction.
6. What is the form of moisture in coal? Individual characteristics?
A :( 1) external moisture? Refers to adhesion of moisture and wetting of the coal surface and the large capillary (diameter> 10-5 cm) holes, it is mechanically retained in the coal, the coal in the air, such The water will evaporate continuously, its content is related to the external conditions, the symbol Mf ; ( 2 ) the internal moisture ? The water adsorbed or condensed in the small pores inside the coal particles, which is physically and chemically combined with the coal, at 105~ at temperature 110 ℃ can be removed, the symbol Minh; (3) crystal water is three coal substance combination of water, to which 200 is at least deg.] C, in order to break out, water can not make aNALYSIS crystallinity?.
7. What are the technical requirements for measuring coal samples with full moisture?
Answer: ( 1 ) The particle size of the sample needs to meet the requirements, and the particle size should be less than 6mm ; ( 2 ) the drying temperature must be controlled as required; ( 3 ) The drying time must be controlled as required.
8. What should I pay attention to when measuring ash ?
Answer: ( 1 ) The sample in the porcelain boat should be flattened, and the thickness of the sample should not be too large;
( 2 ) When ashing, the furnace door can be opened, and the porcelain boat with the sample on the heat-resistant plate is slowly pushed into the mouth of the box-shaped high-temperature electric furnace, and the sample in the porcelain boat is slowly grayed out and smoked. After a few minutes, when the sample no longer smokes, slowly push the porcelain boat into the hot part of the high temperature furnace, and close the furnace door to burn the sample at 815±15 . If a coal sample is ignited during the ashing process, the coal sample will be discarded and must be re-weighed.
( 3 ) The furnace should have a chimney or venting holes to allow the coal sample to exclude combustion products and keep the air flowing during the burning process.
( 4 ) The control system of the high temperature furnace must be accurate. The temperature rise capability of a high temperature furnace must meet the requirements for determining ash.
( 5 ) The ashing time should ensure that the sample is completely ashed at a temperature of 815 ± 15 , but it is also unfavorable to arbitrarily extend the ashing time.
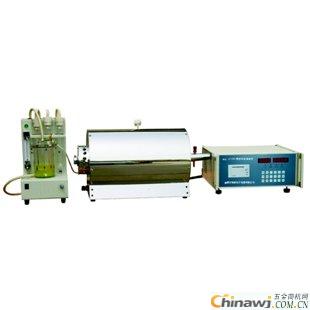
Engine valves are mechanical components used in internal combustion engines to allow or restrict the flow of fluid or gas to and from the combustion chambers or cylinders during engine operation. Functionally, they perform similarly to many other types of valves in that they block or pass flow, however, they are a purely mechanical device that interfaces with other engine components such as rocker arms in order to open and close in the correct sequence and with the correct timing.
The term engine valve may also refer to a type of check valve that is used for air injection as part of the emission control and exhaust gas recirculation systems in vehicles. This type of engine valve will not be addressed in this article.
Engine valves are common to many types of combustion engines, whether they run off a fuel such as gasoline, diesel, kerosene, natural gas (LNG), or propane (LP). Engine types vary by the number of cylinders which are the combustion chambers that generate power from the ignition of fuel. They also vary by the type of operation (2-cycle or 4-cycle), and by the design placement of the valves within the engine [overhead valve (OHV), overhead cam (OHC), or valve in block (VIB)].
This article will briefly describe the operation of engine valves in typical combustion engines, as well as present information on the types of valves and their design and materials. More information concerning other about other valve types may be found in our related guide Understanding Valves.
Engine Valve Nomenclature
Most engine valves are designed as poppet style valves because of their up and down popping motion and feature a conical profile valve head that fits against a machined valve seat to seal off the passage of fluids or gases. They are also called mushroom valves because of the distinctive shape of the valve head. Figure 1 shows the nomenclature for the different elements in a typical engine valve.
Diagram showing the nomenclature of a poppet valve.
Figure 1 - Nomenclature for a standard poppet style engine valve.
Image credit: https://dieselnet.com
The two primary elements are the valve stem and the valve head. The head contains a fillet that leads into a seat face that is machined at a specified angle to match the machining of the valve seat to which it will match. The seating of the valve face to the valve seat is what provides the seal for the valve against combustion pressure.
The valve stem connects the valve to the mechanical elements in the engine that operate the valve by creating a force to move the stem against the seating pressure provided by a valve spring. The keeper groove is used to hold the spring in position, and the tip of the valve stem is repeatedly contacted by a rocker arm, tappet, or lifter that actuates the valve.
Engine Operation
Four stoke or four-cycle internal combustion engines make use of two primary types of valves – the intake valve and the exhaust valve. Intake valves are opened to allow the flow of an air/fuel mixture into the engine`s cylinders prior to compression and ignition, while exhaust valves open to permit the expulsion of exhaust gases from the combustion process after ignition has occurred.
In normal operation, a crankshaft in the engine to which the pistons are attached is tied to a camshaft as part of a valve train arrangement for the engine. The movement of the crankshaft transfers motion to the camshaft through a timing chain, timing belt, or other geared mechanism. The timing and alignment between the position of the crankshaft (which establishes the position of the Piston in the cylinder) and the position of the camshaft (which determines the position of the valves for the cylinder) is critical not only for peak engine performance but also to preclude interference between pistons and valves in high compression engines.
In the intake cycle, the intake cylinder piston cycles downwards as the intake valve opens. The piston movement creates negative pressure that helps draw the air/fuel mixture into the cylinder. Just after the piston reaches the lowest position in the cylinder (known as bottom dead center), the intake valve closes. In the compression cycle, the intake valve is closed to seal off the cylinder as the piston rises in the cylinder to the highest position (known as top dead center), which compresses the air/fuel mixture to a small volume. This compression action serves to provide a higher pressure against the piston when the fuel is ignited as well as pre-heating the mixture to assist with an efficient burning of the fuel. In the power cycle, the air/fuel mixture is ignited which creates an explosion that forces the piston back down to the lowest position and transfers the chemical energy released by burning the air/fuel mixture into the rotational motion of the crankshaft. The exhaust cycle has the piston again rising upward in the cylinder while the intake valve remains closed and the exhaust valve is now open. The pressure created by the piston helps force the exhaust gases out of the cylinder through the exhaust valve and into the exhaust manifold. Connected to the exhaust manifold are the exhaust system, a set of pipes that includes a muffler to reduce acoustical noise, and a catalytic converter system to manage emissions from the engine combustion. Once the piston reaches the top of the cylinder in the exhaust cycle, the exhaust valve begins to close and the intake valve starts to open, beginning the process over again. Note that the cylinder pressure on intake helps to keep the intake valve opened and the high pressure in the compression cycle helps to keep both valves closed.
In engines that have multiple cylinders, the same four cycles repeat in each one of the cylinders but sequenced so that the engine proves smooth power and minimizes noise and vibration. The sequencing of piston movement, valve movement, and ignition is accomplished through the precise mechanical design and electrical timing of ignition signals to the spark plugs that ignite the air/fuel mixture.
Engine Valve Motion
The motion of the engine valves is driven by the camshaft of the engine, which contains a series of lobes or cams that serve to create linear motion of the valve from the rotation of the camshaft. The number of cam lobes on the camshaft is equal to the number of valves in the engine. When the camshaft is in the cylinder head, the engine is called an overhead cam (OHC) design; when the camshaft is in the engine block, the engine is called an overhead valve (OHV) design. Regardless of the engine design, the basic movement of the engine valves occurs by the cam riding against a lifter or a tappet that provides a force that presses against the valve stem and compresses the valve spring, thereby removing the spring tension that keeps the valve in the closed position. This movement of the valve stem lifts the valve off the seat in the cylinder head and opens the valve. Once the camshaft rotates further and the cam lobe moves so that the eccentric portion is no longer directly in contact with the lifter or tappet, the spring pressure closes the valve as the valve stem rides on the centric portion of the cam lobe.
Maintaining the proper valve clearance between the valve stem and the rocker arm or cam is extremely important for the proper operation of the valves. Some minimal clearance is needed to allow for the expansion of metal parts as the engine temperature rises during operation. Specific clearance values vary from engine to engine, and failure to maintain proper clearance can have serious consequences to engine operation and performance. If the valve clearance is too large, then the valves will open later than optimally and will close sooner, which can reduce engine performance and increase engine noise. If the valve clearance is too small, valves will not close fully, which can result in a loss of compression. Hydraulic valve lifters are self-compensating and can eliminate the need for valve clearance adjustments.
Modern combustion engines can use a different number of valves per cylinder depending on the design and the application. Smaller engines such as those used in lawnmowers may have only a single intake valve and one exhaust valve. Larger vehicle engines such as 4-, 6- or 8-cylinder engines may use four valves per cylinder or sometimes five.
Engine Valve Materials
Engine valves are one of the components in internal combustion engines that are highly stressed. The need for reliable engine operation dictates that engine valves be capable of exhibiting resistance to repeated and continuous exposure to high temperature, high pressure from the combustion chamber, and mechanical loads and stresses from the engine dynamics.
The intake valves on internal combustion engines are subjected to less thermal stress because of the cooling effects of the incoming air/fuel mixture that passes by the valve during the intake cycle. Exhaust valves, by contrast, are exposed to higher levels of thermal stress by being in the pathway of the exhaust gases during the exhaust cycle of the engine. In addition, the fact that the exhaust valve is open during the exhaust cycle and not in contact with the cylinder head means the smaller thermal mass of the combustion face and valve head has a greater potential for a rapid temperature change.
Intake valves, because of their lower operating temperatures, are typically made of materials such as chrome, nickel, or tungsten steel. The higher temperature exhaust valves may use more heat resistant metals such as nichrome, silicon‑chromium, or cobalt-chromium alloys.
Valve faces that are exposed to higher temperatures are sometimes made more durable by the welding of Stellite, which is an alloy of cobalt and chromium, to the valve face.
Other types of material used for the fabrication of engine valves include stainless steel, titanium, and tribaloy alloys.
In addition, coatings and surface finishes can be applied to improve the mechanical properties and wear characteristics of the engine valves. Examples of this include chromium plating, phosphate plating, nitride coating, and swirl finishing.
Types of Engine Valves
Besides the characterization of engine valves by function (intake versus exhaust), there are several specific types of engine valves that exist based on design and materials. The primary types of engine valves include:
Monometallic engine valves
Bimetallic engine valves
Hollow engine valves
Monometallic engine valves, as their name implies, are fabricated from a single material that forms both the valve stem and valve head. These types of engine valves provide both high heat resistance and exhibit good anti-friction capabilities.
Bimetallic engine valves, also known as bimetal engine valves, are made by joining two different materials together using a friction welding process to create a valve that has austenitic steel on the valve head and martensitic steel for the valve stem. The properties of each of these steels serve an optimal purpose, wherein the austenitic steel on the valve head provides high-temperature resistance and corrosion resistance, and the martensitic steel for the valve stem offers high tensile strength and abrasive wear resistance.
Hollow engine valves are a special bimetallic valve that contains a hollow cavity that is filled with sodium. The sodium liquifies as the valve temperature rises and is circulated by the motion of the valve, which helps dissipate heat from the hotter valve head. The hollow design facilitates greater heat transfer through the stem than with solid valves because the martensitic stem material is a better conductor of heat than the austenitic head material. Hollow valves are especially suited for use in modern engines that are delivering more power out of smaller, denser engine designs that have higher exhaust gas temperatures which solid valves are not capable of handling. These higher exhaust temperatures are the result of several conditions, including:
A desire for a lean-burn combustion process that reduces greenhouse gas emissions
Engine designs with higher compression ratios and higher combustion pressures which offer greater efficiency
Integrated manifold designs that support turbochargers for more engine performance from smaller engines
There are several other types of engine valve designs. So-called sleeve valves consist of a tube or sleeve that sits between the cylinder wall and the piston, and which slide or rotate driven off a camshaft as with other engine valves. The movement of the sleeve valve causes ports that are cut into the sleeve to align with corresponding ports in the cylinder wall at different points in the engine cycle, thus functioning as a simple engine intake and exhaust valve without the complexities of rocker arms and lifters.
Engine Valve Specifications
Typical engine valves are specified by the parameters outlined below. Note that this data is intended for information purposes and be aware that variations in the parameters used for specifying engine valves may exist from manufacturer to manufacturer. By understanding the specifications, buyers are better equipped to engage in discussions of their specific needs with suppliers of engine valves.
Auto Engine Valve,Car Engine Valve,Engine Valve For Land Rover,Intake And Exhaust Valves
Shijiazhuang Longshu Mechanical & Electrical Equipment Trading Co., Ltd. , https://www.longsbearing.com